In the fast-paced, complex, and busy world of manufacturing, the concept of Kaizen has emerged as a powerful approach for driving continuous improvements and enhancing efficiency. Kaizen, which translates to "change for the better" in Japanese, has become a cornerstone philosophy and a plan of action for organisations seeking to optimise their manufacturing processes.
This article explores the fundamentals of Kaizen, how it can be implemented in manufacturing and highlights its significance in achieving sustainable growth and success.
Implement Kaizen in Manufacturing using this simplified Five Step Process:
- Review your current situation
- Generate ideas for improvements
- Implement the plan/solution
- Analyse results, review, and refine
- Identify the next steps and repeat!
Read on to learn more about how to implement the Kaizen concept in your factory, how to maintain a culture of continued improvement, and read about two real-life examples to read about.
Applying the Kaizen Concept in Manufacturing
At its core, Kaizen embodies the philosophy of continuous improvement through small, incremental changes. It emphasises the importance of ongoing learning, adaptation, and optimisation.
By recognising that even small improvements can have a significant impact over time, manufacturers can create a culture that embraces change, improves productivity and encourages continuous growth. But, how can you implement a continuous improvement strategy in a manufacturing environment? Read on to find out.
The Five Steps of the Kaizen Process
A typical Kaizen initiative in manufacturing often involves the following steps:
Step 01: Identification: Identify a specific area or process that requires improvement.
Step 02:Generate Ideas and Create a Plan for Improvement: Look for actionable ways to address the issues identified in the previous step.
Step 03: Implement the Plan/Solution: Implement the chosen improvement solutions in a controlled and structured manner.
Step 04: Analyse results regularly, review, and refine: Measure the impact of the implemented changes, assess the results, and gather feedback for further improvements.
Step 05: Identify next steps/repeat: Once successful improvements are identified, establish new standards, and develop processes to sustain the gains.
This systematic approach ensures that Kaizen initiatives are well-planned, executed, and integrated into the organisation's culture.
Let's look at each of these five steps of a typical Kaizen process in more detail:
Step 01: Identification
The first step in this process is to review your current situation - processes, strengths, previous mistakes made, etc. This isn’t just for you and the senior team to do - get a range of people from across the business involved at this stage. They likely have a unique and unbiased point of view and could offer feedback that you may not be aware of.
- Map the flow of production and gather data from previous years (if you have machine monitoring implemented already - pull this data to review!)
- Identify where there are bottlenecks and delays in production
- Review any areas in production that don’t add any value
If you don’t yet have the equipment in place to gather data from your production processes, consider machine monitoring software. FourJaw manufacturing software enables manufacturers to understand past performance and optimise for future efficiency. Book a demo with a member of our team to get started.
Step 02: Generate Ideas & Create a Plan For Improvement
Gather your team and present your findings. At this stage, you’re looking for actionable ways to address the issues identified in the previous step. Do this in whichever way you please, but make the most of visual boards, mind mapping, and team collaboration.
- Encourage team members to group up and work together
- Make the most of each staff member’s expertise and experience in niche areas
- Most importantly, be open-minded!
Consider ‘flow’ and ‘process’ Kaizen when deciding your focus areas. Find out more on this below.
Step 03: Implement the Plan/Solution
Once you’ve brainstormed some initial ideas to improve your production processes, implement the chosen improvement solutions in a controlled and structured manner.
Start with the quick wins - i.e. the tasks that will have the biggest impact in the shortest amount of time and with the least effort.
- Delegate the tasks for easier implementation - you can’t do it all!
- Ensure each task has an ‘owner’ - these don’t need to be senior team members
- Choose a date to check in on each task
Step 04: Analyse Results Regularly, Review, and Refine
To keep the momentum going, you must measure the impact of the implemented changes, assess the results, and gather feedback for further improvements from your team.
- Set clear KPIs to review for each action item
- Measure both qualitative and quantitative data
- Schedule Kaizen check-ins monthly, quarterly, or yearly to keep the idea alive and to analyse the results of your improvements
Step 05: Identify the Next Steps and Repeat!
You might not think so, but this is one of the most important steps when implementing Kaizen within your factory. Once successful improvements are identified, establish new standards, and develop processes to sustain the gains. You must create a culture of continuous change, where staff members are always on the lookout for improvements to make.
- Let go of the idea of a ‘finishing date’
- Don’t be afraid to change tactics and direction more than once
- Share your Kaizen values with all new staff members, so everyone is on the same page and culture is maintained
Many organisations implement Kaizen at the same time as other lean methodologies. Read our step-by-step guide on implementing 5S in manufacturing to learn more.
Flow vs Process Kaizen; Which should you use?
Kaizen can be categorised into two types: Flow Kaizen and Process Kaizen.
1. Flow Kaizen
Flow Kaizen focuses on optimising the flow of materials, information, and processes throughout the value stream. It seeks to eliminate bottlenecks, reduce lead times, and enhance overall flow and efficiency.
A value stream map displays all the critical steps in a specific process and quantifies the time and volume taken at each stage, showing the flow of materials and information as they progress through the manufacturing process.
An example of Flow Kaizen is using machine monitoring software to capture machine data allowing you to see your production line in real-time. By doing so, you can identify when jobs are taking longer and proactively remove bottlenecks.
Machine monitoring software captures machine utilisation data and can display a timeline view by machine.
2. Process Kaizen
Process Kaizen zooms in on specific processes or workstations within the value stream. It aims to improve the performance, quality, and productivity of individual processes through targeted enhancements and problem-solving.
A real-life example of process Kaizen is using productivity metrics such as OEE (Overall Equipment Effectiveness), which look at key factors like availability, performance, and quality. Machine monitoring software uses metrics that incorporate OEE considerations, allowing you to run flow and process Kaizen strategies simultaneously.
Both types of Kaizen contribute to overall process improvement, and their application depends on the specific challenges and opportunities within the manufacturing environment.
Illustrative Examples for Implementing Kaizen in Manufacturing
Implementing Kaizen will look different between manufacturers, and the improvements that one business makes might not work for your own.
EXAMPLE 01: Reducing Machine Setup Time
To illustrate the impact of Kaizen, let's first consider a simple example: reducing machine setup time.
-
Identify problems and define goals:
The problem here is the amount of time spent setting up machines; the goal is to reduce this time to improve efficiency.
-
Generate ideas and create an improvement plan:
Analyse the setup process and come up with ideas for reducing the time it takes, such as eliminating unnecessary steps, and implementing efficient practices.
-
Implement the plan/solution:
Following the steps above can significantly reduce the time required to set up machines between different product runs. Implement this in the workplace.
-
Analyse results, and regularly review:
How much time did the above plan save? Could it be improved? Regularly review your processes and refine them for small improvements.
-
Identify next steps/repeat:
Iterate this same process across all areas of your company where efficiency could be improved.
Westley Plastics and KSW Engineering are great case studies highlighting successful Kaizen strategies.
EXAMPLE 02: Production Capacity Constraints
Our next example is a little more detailed and uses a common challenge manufacturers come up against, production capacity constraints.
-
Identify the problem and define goals:
A manufacturer identifies that they have an issue meeting demand, which is caused by production capacity constraints. The management team knows they need to increase production capacity by at least 10% but don’t currently know what they need to do to achieve this goal.
-
Generate ideas and create a plan:
The business has identified that there is a production capacity issue. A goal has been set to increase capacity by 10% to meet the demand. The team discusses what they can do to accurately measure what their current capacity is. Simply buying new machines or running more shifts isn’t a feasible option so the team are to look for a technology solution that will give them the data insight they need to understand what their current capacity is and identify where production bottlenecks are occurring.
-
Implement the plan:
Once the solution and plan have been agreed, the next stage of the Kaizen process is to implement it. In this working example, the business selected a machine monitoring technology to enable them to solve their problem. Once the technology is deployed onto the machines that need monitoring, the business needs to onboard the machine operators and other stakeholders that will be using the solution. It is essential at this stage that everyone understands the problem (capacity constraint), is aware of the goal (increase capacity by 10%) and understands the value and benefit of the solution that has been chosen (easily and accurately capture production data).
-
Analyse results, review, and refine:
A solution such as machine monitoring software can very quickly highlight inefficiencies in a manufacturing process. For example, utilisation data can show the business which machines are being well utilised and in high demand, those that are under-utilised and those whose function perhaps had become redundant.
Using utilisation data as the working example, upon reviewing the data, a management team can use it, to confidently inform changes on the factory floor. For example, the data may highlight that some on-job operations are causing bottlenecks, and therefore the operations manager may look to move some on-job operations to improve cycle times, thus increasing throughput.
Managers can use current and historic machine utilisation trends to benchmark what 'good' looks like. Allowing them to know at a 'glance' if they've had a good day or not.
Another scenario might be where the data can be used to confidently inform commercial decisions. Here are a couple of examples of this in practice.
The management team review the utilisation data over 30 days. It is clear, after reviewing the data that one of their machines isn’t being utilised, and therefore the team deem it surplus to their production needs. The business decided to sell the machine and invest in a more appropriate machine that would meet the growing demands of their customers and help them increase production capacity by 10%.
A secondary benefit to this data was that it helped to inform the decision to stop delivering subcontract work and focus on the company’s direct and more profitable contracts.
-
Identify the next steps and repeat:
Machine monitoring software is designed to be an operational tool that informs manufacturers to make continuous, iterative improvements to their processes. So, as with our working example, a business can continue to benefit from real-time production data, as well as historical trends to know what ‘good’ really looks like on their factory floor. When a trend is falling out of its trendline, take corrective action based on accurate machine data.
In this working example, over six months, the manufacturer saw machine utilisation go from 21.7% to 35.8%, an overall increase in machine utilisation of 14.1%.
How to Successfully Implement Kaizen across the Factory
Successfully implementing Kaizen in the workplace involves several key steps:
- Create a Culture of Continuous Improvement: Foster a culture that values continuous improvement and embraces change as an opportunity for growth.
- Employee Involvement: Involve employees at all levels in the improvement process. Encourage their active participation, feedback, and suggestions for enhancements.
- Measurement and Data Analysis: Establish metrics and systems to measure performance, collect data, and analyse trends. This data-driven approach provides insights for targeted improvements.
- Training and Skill Development: Provide training and skill development opportunities to employees to enhance their problem-solving, analytical, and process improvement skills.
- Visualise and Communicate: Utilise visual management tools and techniques to communicate goals, progress, and areas for improvement throughout the organisation. This ensures transparency and alignment.
Displaying real-time machine utilisation data on the factory floor ensures everyone sees the same data, creating a more informed and aligned workforce.
Achieving a Kaizen culture
To achieve a Kaizen culture in manufacturing, organisations should consider the following factors:
- Set Clear Goals: Define clear goals and objectives for Kaizen initiatives, aligning them with the overall organisational strategy.
- Provide Support and Resources: Allocate adequate resources, including time, training, tools, and technology, to support Kaizen's efforts.
- Embrace Risk-Taking: Create an environment that encourages risk-taking and experimentation. Embrace failures as learning opportunities and encourage innovative thinking.
- Continuous Evaluation: Regularly evaluate the effectiveness of Kaizen initiatives, monitor progress, and make adjustments as necessary. Kaizen is an ongoing journey, requiring constant evaluation and refinement.
We recommend you also refer to the three core Pillars of Kaizen which will support the cultural adoption across the business:
Standardisation
Standardisation ensures consistent and efficient processes across the organisation. By defining best practices, creating standard operating procedures, and promoting adherence to them, manufacturers establish a solid foundation for continuous improvements.
Sustaining Discipline
Sustaining discipline involves maintaining rigour and adherence to standardised processes over time. It requires ongoing training, regular audits/review meetings and management commitment to reinforce the importance of maintaining standards.
Standardisation and sustaining efforts play a key part in the 5S methodology, which is often used in tandem with the Kaizen concept to improve efficiency and productivity. Learn more about the 5S concept in our FREE downloadable guide.
Employee Empowerment
Employee empowerment involves creating a supportive environment where employees are encouraged to contribute their ideas, share knowledge, and actively participate in the improvement process. By empowering employees, organisations tap into their expertise, creativity, and problem-solving capabilities.
These three pillars provide the necessary framework for Kaizen initiatives to thrive and yield sustainable results.
Measure the Impact Of Kaizen in Your Factory With Machine Monitoring Software
As we briefly touched on earlier, technology such as machine monitoring software is a great tool to support continuous improvement methodologies such as Kaizen. An example of this is FourJaw.
FourJaw’s manufacturing analytics software is designed to enable factories to achieve manufacturing excellence and comes with several features that will help drive a Kaizen philosophy. These include:
Machine Monitoring: Machine monitoring software captures productivity and energy usage data in real time. This gives manufacturers actionable insights that can help increase production capacity and understand and reduce their energy consumption which in turn, supports improvements in performance, sustainability and profitability.
OEE Machine Monitoring: Overall Equipment Effectiveness, commonly known as (OEE) is a metric used in manufacturing to measure the efficiency of production equipment, taking into account the Availability, Performance and Quality. FourJaw’s OEE calculation takes into account the impact on the shop floor, making it accessible to manufacturers in both batch manufacturing and more traditional environments where OEE is commonly used such as high-volume manufacturing.
Machine downtime monitoring: Identifying and tracking downtime is essential for any business looking to maximise production. FourJaw captures real-time data to drive continuous improvement in your factory.
Energy Monitoring: Understanding the cost of energy in manufacturing processes allows manufacturers to make informed decisions and process changes that can reduce wasted energy usage, reduce costs, and positively change people's behaviours, making them more aware to make conscious decisions about when to ‘use energy’, which in turn helps to reduce a factories carbon footprint, and in the long term make it more sustainable.
Machine data monitoring software provides manufacturers with a real-time view of their production data. Measuring key production metrics such as utilisation, OEE and energy usage.
Summary: Implementing Kaizen in Manufacturing
Implementing Kaizen, with continuous improvement at its core, and teamwork and employee engagement playing a pivotal role in its success, has become a cornerstone best practice in manufacturing. By implementing the five elements of Kaizen, organisations can drive efficiency, improve quality, and foster a culture of innovation.
By embracing Kaizen as a philosophy, embedding it as a culture and implementing practical strategies, manufacturers can navigate the challenges and unlock the many opportunities sometimes hidden from sight due to the busy and complex nature of manufacturing. In doing so, manufacturers can put themselves in the best possible position to, achieve sustainable long-term growth, retain and attract the best people and stay ahead of the competition.
In conclusion, Kaizen offers a powerful approach for manufacturers to continuously enhance their processes, drive improvements, and adapt to evolving market demands. By embracing the philosophy of Kaizen and implementing its key elements, manufacturers can optimise their operations, engage their employees, and achieve long-term success.
MORE HELPFUL BLOGS
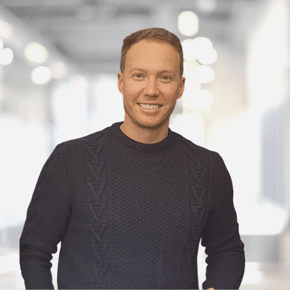