
Testimonials
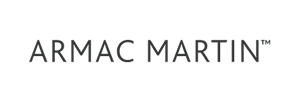
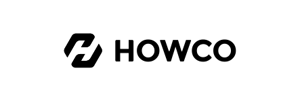
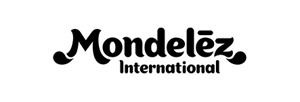
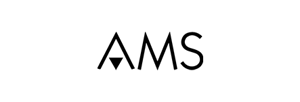
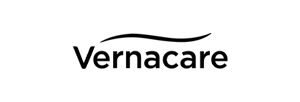
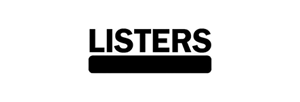

"We have a very personal and strong business relationship with FourJaw and they have helped us identify key areas for improvement and how to carry our business forward. The layout of the data is very well presented and allows us to establish a baseline and then plot growth targets over a timeline." See the full review on Capterra.

“The FourJaw team are incredibly proactive and enthusiastic, ensuring we were in full operation and maximising the value and opportunities from the new system. The FourJaw team regularly checked in and offered additional support sessions for training to keep us on track. A very good onboarding customer experience and one we would certainly recommend, thank you!”

"Excellent software for manufacturing companies to improve utilisation and productivity. Would highly recommend for anyone looking for easy to install and understand CNC machine monitoring".

"You may have been in the position where you think you need to buy another machine. Because you think you’ve got a capacity problem, but now we use FourJaw we can see where we have capacity that I'm not using."

"FourJaw's guidance was instrumental in ensuring our team fully understood the data insights.
This knowledge spurred enlightening conversations, fostering a collaborative environment where best practices were shared, behaviours evolved, and machine utilisation and productivity significantly improved."

"The product is very fast to deploy, and the team is great with supporting us to fit the product just for our individual use. Sure, it might not have all the features at this point that we might want to see, but what I love about it is that it's really a bargain if you look on the value compared to cost."

"FourJaw has been a revelation. We’ve already reduced energy consumption and identified further opportunities for improvement. We know precisely what machines are running and when, what they’re working on, how much energy they use, how long each job takes, and where time is being lost and why."
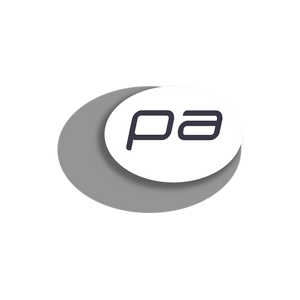
“Due to FourJaw’s machine monitoring insight, we now have an additional capacity that we are now able to keep track of, and as the work builds up we can then plan that in which just gives us another string to our bow: if work comes in and we are going to struggle to get that through during normal hours, we have this additional capacity we can call on.”

"If you’d asked me, before FourJaw, what the cycle times were, I genuinely would not have known. I now have a better feel for what’s involved, which has allowed us to change our production processes."

"We had a strong business before FourJaw but limited visibility of shop floor operations. We've addressed that with FourJaw, and the response from management and machine operators has been positive. Everyone has clarity of what needs achieving and has bought into our plans to improve productivity and profitability."
Manufacturing Productivity
Starts Here.

“FourJaw's machine monitoring solution has helped to quantify our initial thinking and put some value to it so that we could make more-informed data-based decisions. The recent product enhancements have made FourJaw a solution that is delivering real benefit from the top floor to the shop floor, it’s the team’s operational tool.”
.png?width=70&name=Happy%20(5).png 1x, https://25959638.fs1.hubspotusercontent-eu1.net/hub/25959638/hubfs/Happy%20(5).png?width=105&name=Happy%20(5).png 1.5x)
"FourJaw was an easy investment to make and a giant leap forward in our digitisation journey. It has been adopted as part of the culture of our organisation, improving efficiency and communication and providing objective data to inform production schedules, operational improvements and machine investment strategies."

“It’s an absolutely fabulous tool to use and has become an essential aspect of our production planning processes. We are also using it for pricing. Sometimes, especially with a new job, we estimate production time based on similar components, but now we can see instantly how long the job actually takes.
The simplicity of using FourJaw's downtime monitoring software has convinced us to roll it out across the entire shop floor. It’s literally opening our eyes to see things for the first time.”

"I wish I had more time in my day to find faults with FourJaw, it really is simple and straightforward to use. My only problem is I'm too busy too implement the latest functions!"

“In the CNC cell, we have doubled the number of operatives because of the efficiencies we have been able to make. So we are employing more people in the cell, producing more products and the cost per unit of the product has decreased. That’s a big win.”

"FourJaw is the tool we use to maintain a ‘drumbeat’ of improvement and create a healthy, competitive environment to keep trying to do better"

"FourJaw facilitated conversations which were used to inform and educate operators, leading to a greater sharing of best practices, changed behaviours, and enhanced machine utilisation and productivity."
Manufacturing Success Stories.
From 19% to 47% - How this factory Transformed Machine Productivity
Fernco transforms factory insight and productivity
Aerospace Manufacturer, AVPE Systems increases factory uptime by 30%
Global Healthcare Manufacturer, Vernacare turns to smart technology to drive efficiency
Ready to
Learn More?
See how FourJaw's plug-and-play analytics can help you turn machine data into real productivity gains. What would you like to do next?
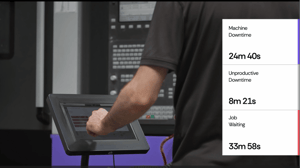