Your Path to Maximum Manufacturing Productivity
Our team is here to support you, from the initial onboarding process right through to identifying improvement opportunities and working with you to measure the effectiveness of the process improvements in your manufacturing business.
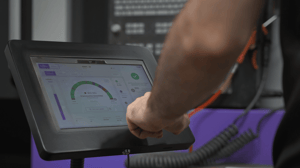
Top Tips For A Successful Roll-Out

Meet The FourJaw Customer Success Team
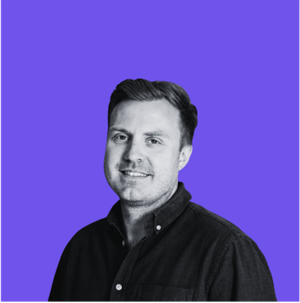
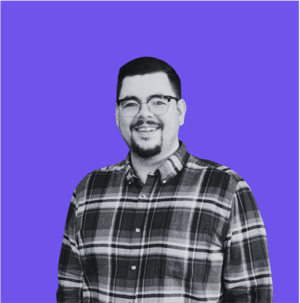
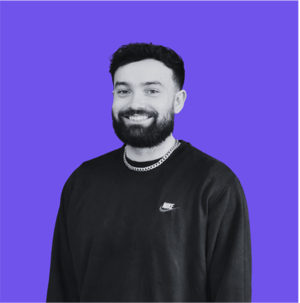
FourJaw Productivity Improvement Customer Journey
Start
Our process for getting you configured and set up with FourJaw.1. Guided Tour
A guided tour of the platform that will be tailored to your manufacturing processes and challenges.
2. Order Placed
Once the order is placed, we aim to dispatch your hardware within five working days.
3. Key Details
Provide details of the key people involved, the machines being monitored and the Wi-Fi details.
4. Installation
Plug-And-Play hardware installed by your own, qualified, electrician.
EMBED
Our process to validate your data, train and drive cultural adoption.5. Data Classification
Confirm Data Classification is correct, per machine, calibrating FourJaw to your machines.
6. Stakeholder Training
A virtual training session to get you and the key stakeholders confident with the platform.
7. Data Analysis
Collect and analyse machine data to gain an understanding of the ‘current state’.
GROW
Our process to analyse, refine and optimise to drive continuous improvement and ROI.8. Optimise
Explore utilisation, OEE, and machine downtime reasons, and make changes to processes to drive improvement.
9. Measure & Refine
After 2-4 weeks measure and refine based on data insight following changes from step 08.
10. Improvement & ROI
Look at the productivity improvements achieved, and calculate an ROI to support the business case for further roll-out.
Technology Trusted by Manufacturers of all Sizes
Taking your first step into the world of smart factory technology? We've put together a number of case studies showcasing how manufacturers who were once in your position have benefited from our machine monitoring platform.
Need Support?
Visit Our Knowledge Base
Find answers to common questions and keep up to date with the latest product release features at help.fourjaw.com
Contact The Team
You can contact our customer support team Monday-Friday, 8:00 am until 5:30 pm (GMT), simply complete the form or contact them via the details below.
- ADDRESS: Block 4, Level 2, Pennine Five, 18 Hawley Street, Sheffield, S1 4WP
- PHONE: +44 (0) 114 400 0158
- EMAIL: info@fourjaw.com
- WEB: www.fourjaw.com