.png?width=300&name=Increase%20Production%20Capacity%20%20(2).png)
Deliver Precision. Minimise Delays
Real-time alerts and machine-level data allow teams to act quickly, fix issues fast, and keep lines moving and machines running.
Pinpoint inefficiencies, highlight bottlenecks, and enable fact-based decisions that support lean initiatives.
From stamping to assembly, processes must align tightly to avoid rework and waste. FourJaw provides real-time insight into production stages, so teams can quickly spot slowdowns or mismatches.
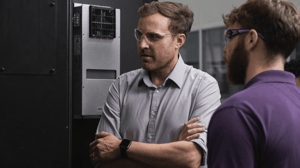
Optimise Like an F1 Team
In manufacturing, operators are the drivers—skilled, focused, and fast. Your job? Be the pit crew. Ready to act, optimise performance, and keep production on track.
FourJaw gives you the real-time data to spot issues, fine-tune processes, and keep your team ahead of the competition.
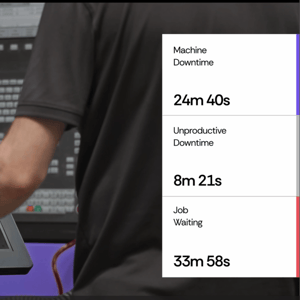
Stay Informed. Stay on Track.
FourJaw removes the guesswork from production with live tracking and smart alerts, enabling you and your teams to stay informed and on track to deliver on time, every time.
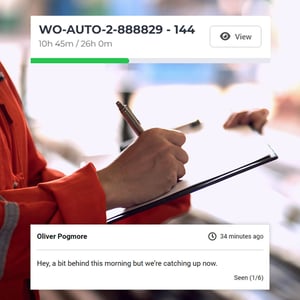
Every Second Counts. Every Pound Matters.
FourJaw pinpoints underperforming machines and processes, helping you cut waste, boost efficiency, and protect your profit margins.
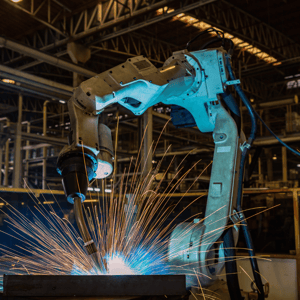
Manufacturing Productivity
Starts Here.
How it Works
Tracking machine downtime is simple with FourJaw’s plug-and-play solution. Easily determine and tackle top downtime causes to keep production lines moving.
Clip the sensors to the machine's power cables.
Smarter Shifts. Start Here
Manual data capture is slow and unreliable.
FourJaw captures real-time machine data automatically, providing instant, accurate insights to spot inefficiencies and take action fast.
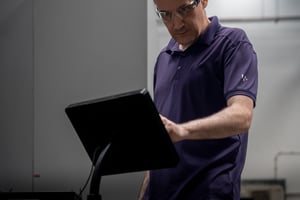
FourJaw's Features
From productivity to sustainability, FourJaw helps automotive manufacturers stay ahead with real-time insights.
Gain capacity by improving processes and removing bottlenecks.
Simplify planning and communication for a more efficient factory floor.
Cut energy waste, streamline processes, and shrink your carbon footprint.
Ready to
Learn More?
See how FourJaw's plug-and-play analytics can help you turn machine data into real productivity gains. What would you like to do next?
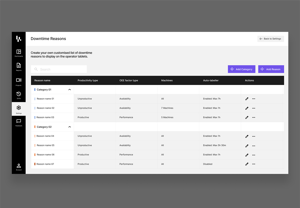