
OEE Monitoring Software
Monitor Overall Equipment Effectiveness in real-time.
Measure OEE without the Hassle
Measure what matters.
FourJaw calculates OEE and other key performance metrics in real time, helping you benchmark, track improvement, and maximise machine utilisation.
Get an OEE score by machine, cell, production line or factory, in real-time and over time.
Understand the underlying reasons for any production losses and take corrective action.
Use accurate OEE data to inform process and behavioural changes to drive improvement.
OEE
Features
OEE Trends
Know what 'good' OEE looks like in your factory
- See your overall OEE trend or view it by Performance, Availability or Quality, by hour/day.
- Zoom out or In - see your OEE trend by factory, cell, production line or machine.
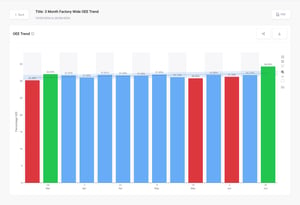
See Your top downtime reasons
Not all downtime is equal. Track time in each state, productive or unproductive.
Use Downtime Pareto to reveal the top causes, so you know exactly where to focus to boost availability and performance.
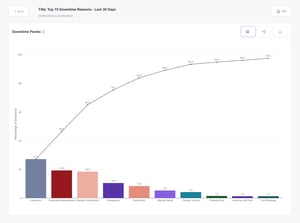
OEE By Shift
See Overall Equipment Effectiveness by shift.
- See your OEE score by shift and look into the data insight to understand which shifts are more productive and why
- Make process changes to improve shift efficiency
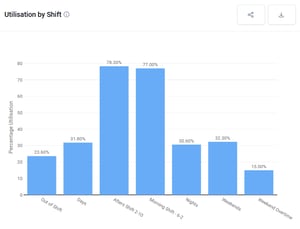
Customers see an Av. increase of +20% in manufacturing productivity
According to Make UK, 74% Of Manufacturers Cite Improving Productivity As A Key Driver For Investment.FAQ
Didn’t find what you were looking for? Send us a message via the contact form and we’ll make sure it gets to the right person.
The OEE measure in manufacturing looks at three factors; Quality, Performance and Availability. FourJaw's machine monitoring platform is designed to help identify, measure and improve how productive a production line (or machine) is.
Therefore if you're looking to start or improve your current OEE measures, then our machine monitoring platform can help you with your manufacturing performance and availability.
OEE in FourJaw tracks the performance and availability of your machine using the downtime reasons logged by machine operators. To do this, you need to choose an OEE category for each of your downtime reasons.
Anything that means that your machine is not available to use because it is broken, undergoing maintenance or being reprogrammed etc. is set to downtime OEE category Availability. Everything else is set to performance.
Examples of Availability Downtime reasons include: Machine fault, Tool broken, Set Up, Unplanned maintenance etc
FourJaw 's OEE monitoring system provides several benefits, ideally suited for Production Managers, including:
- See trends in OEE / Availability / Performance / Quality over 3 or 6 months – so that you can set targets and celebrate success.
- See OEE broken down by Factory, Cell or Machine so that you can focus continuous improvement efforts in the right place.
- Drill down and see what downtime reasons are affecting performance and availability so that you can try and solve issues.
- See how productivity differs across different shifts.
FourJaw's OEE monitoring software provides two key benefits to factory floor managers. These include:
- Ability to investigate cycle times and drive reductions by comparing cycle times on different machines and across shifts.
- Ability to investigate the number of stops per shift and drive reduction by comparing different machines and shifts.
FourJaw’s OEE software reports on three key metrics Availability, Performance, and Quality. The results of these metrics are used to generate an overall OEE percentage.
OEE and Performance, Availability and Quality all start at 100% and are reduced when issues are logged. OEE calculations should not result in figures over 100%.
Availability
The availability measure monitors a machine, cell, or factory's actual runtime versus planned runtime. This data can be used to highlight how much-unplanned downtime and quality issues are impacting your factory's productivity.
Availability = ((Total time in the period – downtime logged to availability issues) / Total time in the period) x 100
Performance
The performance measure reports on output productivity by comparing the number of units produced in a time period versus the number of units which could theoretically be produced.
Performance = ((Total time in the period – downtime logged to performance issues) / Total time in the period) x 100
Quality
The quality measure is the ratio between good units produced and the actual number of units produced.
Quality % = ((Uptime logged in time period - time labelled bad)/Uptime logged in time period) x 100
Ready to
Learn More?
See how FourJaw's plug-and-play analytics can help you turn machine data into real productivity gains. What would you like to do next?
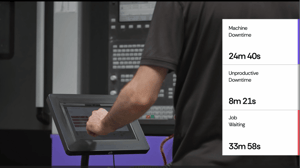