
Machine Monitoring Software
Award-winning manufacturing monitoring technology. Capture and visualise key production data with ease.
What Makes FourJaw Different?
Automatically capture real-time production data from any machine with our machine monitoring software.
See your factory’s production data in real time. Monitor live production data from anywhere, at any time.
Turn your production data into clear, actionable insights to drive continuous improvement. Make informed decisions to increase productivity, remove bottlenecks and drive sustainable growth.
Real-time downtime alerts enable you to proactively manage production inefficiencies before they escalate. Keeping your operations efficient, machines running and production schedules on track.
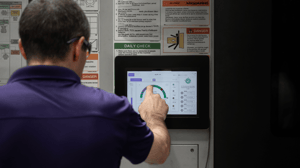
Machine Monitoring, Installed in minutes.
FourJaw works on ANY Machine, regardless of age or type.
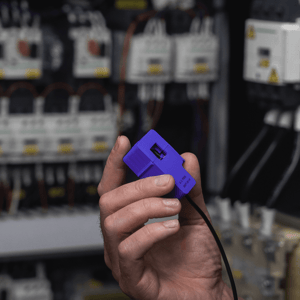
Clip the sensors to the machine's power cables.
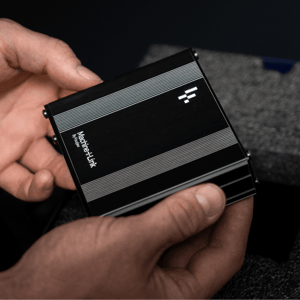
Connect the MachineLink IoT device to WiFi and mains power.
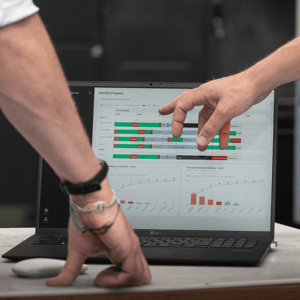
Use data insights to start identifying and removing inefficiencies.
What Makes FourJaw Different?
Machine monitoring software designed to seamlessly work with any mains powered manufacturing machines.
*FourJaw works with almost any machine that draws power. Because FourJaw doesn’t rely on PLC integrations, it’s brand-agnostic, making it ideal for manufacturers with machines of varying ages, brands, and types.
Software Features
See the biggest drivers of machine downtime and wasted energy at a glance, enabling you to focus on the most impactful solutions to keep your machines running smoothly.
Machine Utilisation
FourJaw provides standardised machine utilisation data, enabling you to identify inefficiencies and optimise existing resources.
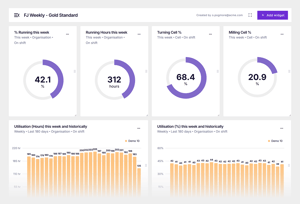
Production Timeline
Identify production bottlenecks in real time with our Timeline View, and drill down to see exactly where production is stalling.
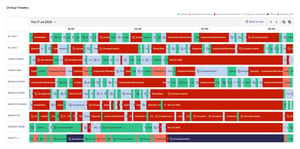
Energy Consumption Reports
Factories often waste energy unnecessarily, while facing increasing pressure to meet sustainability goals. FourJaw's sustainability features help you tackle both challenges at once.
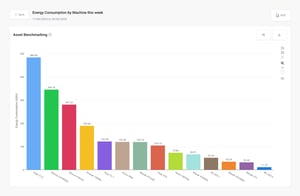
Try an Interactive Guide
Get instant access to FourJaw’s Interactive Intro and see how it transforms manufacturing efficiency
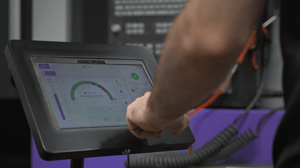


See FourJaw In Action
Share your company details to request a personalised demo and discover the full potential of your factory.
Frequently Asked Questions
FourJaw's machine monitoring solution is designed for use on all types of manufacturing equipment. Generally, if it has an electrical current, FourJaw can tell you how productive it is (and how much energy it uses).
The system connects machines using non-invasive sensors that link to our MachineLink IoT hardware.
When the MachineLink detects machine downtime, it automatically prompts the operator via the FourJaw tablet to select the reason for the downtime from a predefined list (customisable by you).
The data is then displayed on FourJaw's web-based dashboard, allowing managers to make data-driven decisions in real-time.
FourJaw's machine monitoring system is designed for use on all types of manufacturing equipment, including.
- CNC machines
- Lathes & milling machines
- Presses & injection molding machines
- Assembly lines
- Fabrication equipment
Generally, if it has an electrical current, FourJaw can tell you how productive it is (and how much energy it uses).
Where conventional systems might read any spindle movement as "productivity", FourJaw accurately detects genuine, money-making productivity. For example, FourJaw can detect when a CNC machine is cutting metal, by observing the rise in current usage during actual work.
This not only provides a more accurate measure of machine efficiency but also ensures consistency in data across all machines, facilitating better decision-making across your factory.
FourJaw captures downtime data through a combination of its MachineLink hardware and tablets mounted on the machines.
When a MachineLink detects downtime, it automatically prompts the operator via the tablet to select the reason for this downtime from a predefined list.
This process is quick and non-disruptive, designed to minimise interruption to the operator's workflow.
By simplifying the input method to just a few taps, FourJaw ensures that accurate downtime reasons are recorded with minimal effort, enabling a comprehensive analysis of machine productivity and downtime causes without impeding your operators.
Yes. Unlike traditional machine monitoring solutions, we designed our machine monitoring platform to be accessible, not only did we make it easy to install (minimising disruption to your factory floor) but we also made it affordable.
We offer monthly payment plans and you can install it yourself, so there are no high upfront installation costs often associated with traditional machine monitoring solutions