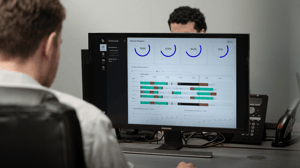
Identify underutilised assets and optimise resource allocation.
Identify and address the top causes of downtime with detailed downtime reports.
Drive continuous improvement: optimise processes for speed, quality and cost savings.
Machine Productivity Features
Drive productivity across your manufacturing operations. Whether you're looking to make processes faster, better or less costly, our productivity tools have you covered.
Machine Utilisation
FourJaw provides standardised machine utilisation data, enabling you to identify inefficiencies and optimise existing resources.
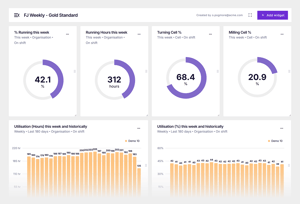
Production Timeline
We make manufacturing Production monitoring easy. Get a true view of machine downtime, see overall production performance, and use the insight to anticipate issues ahead of the next shift.
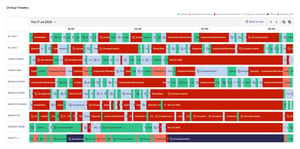
OEE
Enhance operational efficiency and reliability in manufacturing processes by understanding your overall equipment effectiveness. Get a real time view of productivity to get a true view of asset utilisation and capacity.
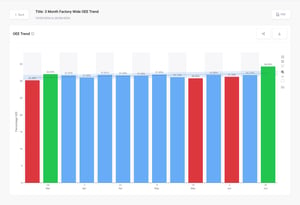
Downtime Reporting
Understand the top causes of machine downtime and their affect on costs and performance. Take corrective action to target downtime where it matters most using pareto analysis.
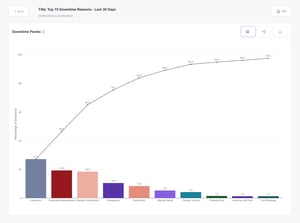
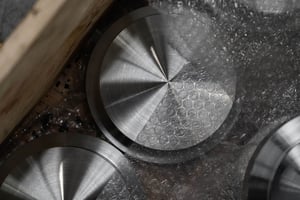
FourJaw is helping us move towards 4.0 based on our S&OP. It allows us every month to analyse with the directors to see our strengths and weaknesses and plan forward based on what we find.
FourJaw has delivered a significant and sustained improvement in the productivity levels we're getting from our manufacturing centres resulting in a 30% overall increase in uptime.
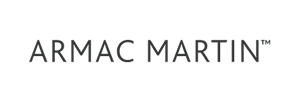
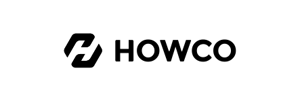
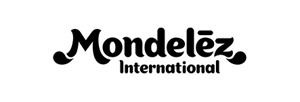
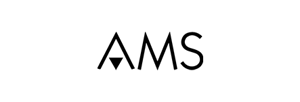
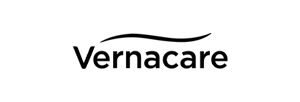
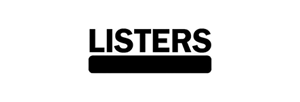
FourJaw's Features
Everything you need to streamline and optimise processes to grow your business.
Streamline processes to cut costs, boost speed, and enhance efficiency.
Simplify planning and communication for a more efficient factory floor.
Cut energy waste, streamline processes, and shrink your carbon footprint.
Manufacturing Success Stories.
From 19% to 47% - How this factory Transformed Machine Productivity
Fernco transforms factory insight and productivity
Aerospace Manufacturer, AVPE Systems increases factory uptime by 30%
Global Healthcare Manufacturer, Vernacare turns to smart technology to drive efficiency
FAQ’s
Here's some of the most common questions we get asked from manufacturers who are looking to install machine monitoring software within their manufacturing operations.
By leveraging the capabilities of machine monitoring systems, manufacturers can gain valuable insights, enhance control over their processes, and systematically eliminate waste, thus achieving greater efficiency and productivity.
Many manufacturers use machine monitoring as part of their wider continuous improvement initiatives. As the data is ideal to help identify and inform what machines and processes can be improved.
The importance of manufacturing productivity lies in its impact on overall operational performance, competitiveness, and profitability.
Manufacturing productivity refers to the efficiency and output of a manufacturing process in relation to the resources invested, such as labour, time, energy, and materials. It is a measure of how effectively a factory or production facility converts inputs into outputs, typically measured by the quantity and quality of goods produced within a given time frame. You can read our blog that looks at the importance of manufacturing productivity here.
There are many methodologies and tools that manufacturers can use to help manage and improve productivity. Perhaps most famously is Kaizen, which originated from Japan and is infamous with the Toyota Production System.
Here are a few of our recommendations:
Kaizen (Continuous Improvement)
Lean & Agile Manufacturing principles
Absolutely. We've tailored our machine monitoring system to ensure it's usable by manufacturers across the board, which includes ensuring compatibility with machines of every age, make, or model. This means even machinery that's decades old can be upgraded to a "smart machine," enabling you to gain insights into the productivity of your equipment.
FourJaw captures downtime data through a combination of its MachineLink hardware and tablets mounted on the machines.
When a MachineLink detects downtime, it automatically prompts the operator via the tablet to select the reason for this downtime from a predefined list.
This process is quick and non-disruptive, designed to minimise interruption to the operator's workflow.
By simplifying the input method to just a few taps, FourJaw ensures that accurate downtime reasons are recorded with minimal effort, enabling a comprehensive analysis of machine productivity and downtime causes without impeding your operators.
Yes, we have a number of manufacturing success stories that provide real-life examples of how manufacturers have benefited from our machine monitoring platform.
Here are some examples that focus on productivity improvement:
Aerospace Manufacturer sees factory uptime increase by 30%.
Global aerospace component manufacturer finds 273 lost productive hours per week.