In the competitive landscape of modern manufacturing, the pursuit of efficiency and waste reduction is paramount. Lean manufacturing principles, derived from the Toyota Production System, focus on eliminating eight specific types of waste: defects, overproduction, waiting, non-utilised talent, transportation, inventory, motion, and excess processing.
This article explores the 8 wastes of lean manufacturing, providing examples of each and looks at what tools and techniques can be strategically applied to each of the eight wastes, offering practical solutions to optimise productivity, reduce costs, and improve overall process efficiency.
The 8 Wastes of Lean Manufacturing
Lean manufacturing is a methodology that focuses on minimising waste within manufacturing systems while simultaneously maximising productivity. It is derived mostly from the Toyota Production System (TPS) and its focus is on reducing waste and improving processes. The eight types of waste in lean manufacturing are often remembered by the acronym "DOWNTIME". We'll explore each of these in more detail.
Communicate the 8 Wastes of Lean Manufacturing on your factory floor. Download our free posters.
01. Defects:
Description: Products or materials that are not up to quality standards, leading to rework or scrap.
Application: Implement quality control measures, conduct regular inspections, and use root cause analysis to prevent defects.
Effective methods/tools to use:
Root Cause Analysis: Use tools like Fishbone Diagrams, 5 Whys, and Pareto Analysis to identify the root causes of defects.
Quality Control Systems: Implement Statistical Process Control (SPC) and Six Sigma methodologies to monitor and improve process quality.
Poka-Yoke (Error Proofing): Design processes and tools to prevent errors before they occur.
02. Overproduction:
Description: Producing more than is needed or producing it too early, leading to excess inventory.
Application: Utilise Just-In-Time (JIT) production to produce only what is needed when it is needed, aligning production closely with demand.
Effective methods/tools to use:
Just-In-Time (JIT) Production: Align production schedules closely with customer demand to produce only what is needed when it is needed.
Pull Systems (Kanban): Use visual signals to trigger production and inventory replenishment only when necessary.
Demand Forecasting: Improve forecasting accuracy to better match production with actual demand.
03. Waiting:
Description: Idle time when resources are not in use, leading to delays and inefficiencies.
Application: Streamline processes to ensure smooth workflow, reduce machine downtime through preventive maintenance, and balance workload among workers.
Value Stream Mapping: Identify and analyse process flows to pinpoint and eliminate bottlenecks and delays.
Workload Balancing (Heijunka): Level out the production schedule to reduce waiting times and ensure a smooth flow of work.
Total Productive Maintenance (TPM): Implement a maintenance strategy to reduce machine downtime and ensure equipment reliability.
04. Non-utilised Talent:
Description: Underutilising people’s skills, capabilities, and talents.
Application: Empower employees, provide training, encourage suggestions for process improvements, and involve employees in decision-making.
Effective methods/tools to use:
Employee Empowerment: Involve employees in decision-making processes and encourage them to contribute ideas for improvements.
Training and Development: Provide ongoing training to develop employees' skills and ensure they are utilised effectively.
Kaizen (Continuous Improvement): Foster a culture of continuous improvement where employees are encouraged to identify and eliminate waste.
05. Transportation:
Description: Unnecessary movement of products or materials between processes.
Application: Optimise plant layout to reduce travel distance, use efficient material handling systems, and group processes that are frequently used together.
Effective methods/tools to use:
Factory Layout Optimisation: Design the plant layout to minimise unnecessary movement of materials and products.
Material Handling Systems: Use efficient material handling equipment such as conveyors, automated guided vehicles (AGVs), and cranes.
Point-of-Use Storage: Store materials and tools close to the point of use to reduce transportation distances.
Optimising factory floor layouts can help reduce the time spent on moving around the factory floor.
06. Inventory
Description: Excess products and materials are not being processed.
Application: Implement inventory management systems like Kanban, reduce batch sizes, and improve forecasting and planning.
Effective methods/tools to use:
Inventory Management Systems: Implement systems like Kanban, JIT, and Economic Order Quantity (EOQ) to control inventory levels.
Supplier Collaboration: Work closely with suppliers to ensure timely delivery of materials and reduce the need for excess inventory.
Batch Size Reduction: Reduce batch sizes to lower inventory levels and increase production flexibility.
07. Motion:
Description: Unnecessary movements by people (e.g., walking, reaching, bending) that do not add value.
Application: Design ergonomic workstations, provide appropriate tools within easy reach and use techniques like 5S to organise the workplace.
Effective methods/tools to use:
5S Methodology: Implement 5S (Sort, Set in Order, Shine, Standardise, Sustain) to organise the workplace and eliminate unnecessary movements.
Ergonomic Workstation Design: Design workstations to minimise reaching, bending, and other non-value-added motions.
Standardised Work: Develop and use standardised work instructions to ensure consistent and efficient task performance.
08. Excess Processing:
Description: Performing more work or using more resources than necessary.
Application: Standardise processes, simplify procedures, and eliminate redundant steps.
Effective methods/tools to use:
Process Standardisation: Simplify and standardise processes to eliminate unnecessary steps and ensure consistency.
Value Analysis: Evaluate each step in the process to determine if it adds value to the customer and eliminate steps that do not.
Lean Six Sigma: Use Lean Six Sigma tools to analyse and streamline processes, reducing unnecessary processing.
General Best Practices for Lean Manufacturing
-
Kaizen Events: Conduct regular Kaizen events to identify, analyse, and eliminate waste in specific processes.
- Continuous Improvement Culture: Foster a culture where continuous improvement is encouraged and rewarded.
- Visual Management: Use visual controls like dashboards, charts, and signs to monitor performance and highlight areas of waste.
- Leadership Commitment: Ensure that leadership is committed to lean principles and actively supports waste reduction initiatives.
How Machine Monitoring Supports Lean Manufacturing
Manufacturing technologies such as machine monitoring can significantly contribute to eliminating the ‘8 Wastes of Lean Manufacturing’ by providing real-time data, insights, and control over manufacturing processes. Here’s how it can help address each of the ‘8 Wastes’:
Defects:
Real-Time Quality Monitoring: Machine monitoring systems can detect deviations in process parameters that might lead to defects, allowing immediate corrective actions.
Predictive Maintenance: By monitoring machine health, potential issues can be identified before they lead to quality problems, reducing the occurrence of defects.
Data-Driven Root Cause Analysis: Historical data from machine monitoring can be used to analyse and understand the root causes of defects, leading to more effective solutions.
Machine monitoring provides real-time production data that allows operations and production teams to ensure work in progress is on track and if not, identify where bottlenecks are.
Overproduction:
Demand-Driven Production: Machine monitoring enables synchronisation with real-time demand, ensuring production is aligned with actual requirements.
Production Scheduling: Accurate data from machine monitoring helps in creating more precise production schedules, avoiding the pitfalls of overproduction.
Waiting:
Downtime Reduction: Monitoring systems provide alerts and diagnostics for machine downtime, allowing for quick resolution and minimising waiting times.
Workflow Optimisation: Data on machine utilisation and performance can help identify bottlenecks and streamline workflows to reduce idle times.
Read a case study to find out how they saved more than 270 lost productive hours per week due to machine downtime.
Non-utilised Talent:
Skill Optimisation: Machine monitoring data can highlight areas where human intervention is most needed, allowing better allocation of skilled labour.
Empowering Workers: Providing operators with real-time data empowers them to make informed decisions, enhancing their contribution to the process.
Providing machine operators with tools such as machine monitoring enables them to make informed decisions in real-time, enabling them to get more out of their machines and identify areas for improvement.
Transportation:
Optimised Material Flow: Machine monitoring can track the movement of materials and products, helping to optimise factory layouts and reduce unnecessary transportation.
Integration with AGVs: Automated Guided Vehicles (AGVs) and other material handling systems can be integrated with machine monitoring to ensure efficient transportation.
Inventory:
Inventory Control: Real-time data on production rates and machine status helps in maintaining optimal inventory levels, reducing excess inventory.
Just-In-Time Manufacturing: Machine monitoring supports JIT practices by providing accurate data to synchronise production with demand, minimising inventory holding costs.
Accurate production capacity planning is critical to ensure you have just the right amount of inventory on hand to be able to fulfil customer orders.
Motion:
Ergonomic Improvements: Data from machine monitoring can identify inefficiencies in operator movements, leading to ergonomic improvements and reduced unnecessary motion.
Process Mapping: Monitoring data helps create detailed process maps that can be used to streamline workflows and reduce excessive motion.
Excess Processing:
Process Standardisation: Monitoring systems can ensure that processes are performed consistently, reducing the likelihood of unnecessary steps.
Continuous Improvement:
Ongoing data collection and analysis from machine monitoring can identify opportunities to streamline processes and eliminate excess processing.
Machine Monitoring Implementation Tips
-
Training and Involvement: Train and engage shop floor staff and key stakeholders on how to use monitoring systems and explain why you’re using them. Involve them in interpreting data and implementing improvements and feedback on how the data is being used, to create a continuous feedback loop of communication.
-
Continuous Monitoring and Feedback: Establish a culture of continuous monitoring and feedback to ensure ongoing improvements and waste reduction.
Managing and removing the eight wastes from a manufacturing process requires a systematic approach that involves various lean tools, techniques, and cultural changes.
By leveraging the capabilities of machine monitoring systems, manufacturers can gain valuable insights, enhance control over their processes, and systematically eliminate waste, thus achieving greater efficiency and productivity.
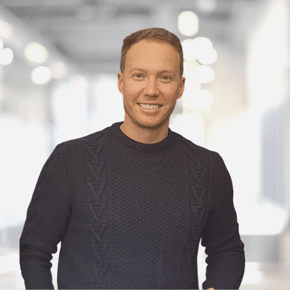