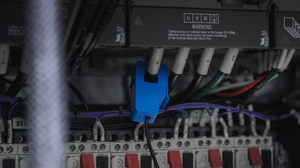
Energy Monitoring Software
Purpose Made for Manufacturers
Reduce wasted energy. Improve Sustainability.
Cut Energy Waste.
Increase Margins.
FourJaw’s Energy Monitoring gives you the data to see exactly where energy is being used and wasted so you can take action that lowers costs and supports your sustainability goals.
Unlike standalone systems, FourJaw links energy data with machine performance, helping you drive a factory that’s not only greener, but more productive and profitable.
By machine, cell, production line or factory, in real-time and over time.
Understand which machines waste energy in downtime.
See how energy usage translates to costs and carbon footprint to motivate change.
Simple Energy Monitoring
By combining energy usage data and machine usage data, FourJaw's Energy Monitoring feature provides a number of financial, process, cultural and environmental benefits.

Understand the cost of energy used by machine, cell, production line or factory. Make informed cost-reduction decisions.
Understand whether energy is wasted on downtime or consumed by productive work. Learn more about downtime tracking.
Make informed decisions about processes to drive energy-efficient and productive manufacturing.
Drive behaviour change to reduce energy waste and support continuous improvement in the factory.
Understand your carbon footprint by machine to support your sustainable manufacturing initiatives.
Clip-on sensors for hassle-free installation and minimal disruption.
Reduce Wasted Energy Costs And Reduce Your Carbon Footprint
Energy Consumption
Understand how much energy is used by machines, cells or factories.
- Track energy usage trends and make informed decisions to reduce usage and improve efficiency
- Energy consumption in some operations is proportionally a large amount of the overall manufacturing costs. Understanding the cost on a part-by-part basis enables more accurate costing meaning you can understand the margin quicker
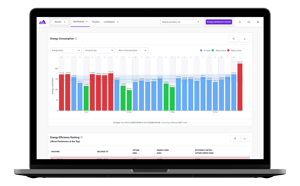
Carbon Footprint
Understand your carbon footprint by machine.
- Provide evidence of energy use reduction to regulatory bodies e.g. Climate Change Agreements with the Environment Agency (UK)
- Assess the carbon impact of equipment to inform sustainability decisions and meet benchmarks
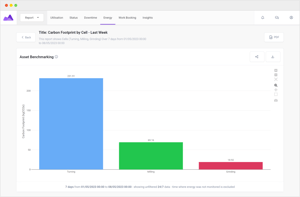
Cost of Energy Used
Understand how much the energy you've used has cost.
- Reduce the cost of production by understanding the cost of energy and reducing unproductive downtime
- Understand what work is most profitable and how to quote more accurately
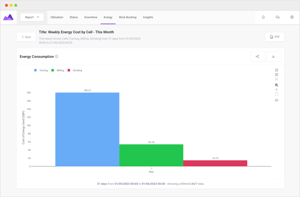
Energy Efficiency Ranking
Rank machines by energy efficiency.
- FourJaw's Energy Efficiency Metric combines energy use and productivity data to rank machines by energy efficiency
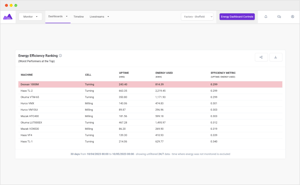
Frequently Asked Questions
Need to know something that’s not covered here? Just use the contact form and we’ll come back to you.
The accuracy of the energy use values will depend on the accuracy of the power factor of your machines plus the accuracy of the current clamp measurement.
FourJaw current clamps have been independently tested and in the range of 1 - 100 Amps, the accuracy is +/- 5.5%.
Energy monitoring in this way is accurate enough to show you trends and anomalies. For applications requiring more accurate data on energy monitoring, you can scale the energy use stated by FourJaw to that given by an accurately calibrated ammeter by changing the power factor of the machine.
Current Range
The current clamps we use work on any machine where each phase has a current draw from 50mA-100A.
3-phase or 1-Phase
If your machine uses 3-phase electricity, simply clamp around one phase of the main incoming supply and make sure the machine has 3-phase chosen within the FourJaw energy settings. If 1-phase, clamp to either the live or neutral, but not both at the same time, and choose 1-phase in settings.
Age, Make and Model
The age, make or model of the machine doesn’t impact the efficacy of the FourJaw platform.
Exceptions
Sometimes to optimise productivity and energy monitoring at the same time, the current clamps need to be moved to be on both the power supply and a particular spindle. If this is the case, our support team will work with you to get this right.
We calculate power usage as follows:
Single Phase
P = pf × I × V / 1000
In this formula, the amount of power - P (in kW) is equal to the power factor of the load (pf) multiplied by the phase current measured in Amps (A), multiplied by the Root Mean Square (RMS) line-to-line voltage (V), and divided by 1000.
3-Phase
P (kW)= √3 × pf × I × V /1000
The power - P (in kW) equals the square root of three (√3) multiplied by the power factor (pf) multiplied by the current in Amps (A), multiplied by the Root Mean Square (RMS) line-to-line voltage (V) divided by 1000.
To calculate the cost:
We multiply the power used by the cost per kWh given on the settings page.
To calculate the carbon footprint:
We multiply the power used by the kilograms of carbon equivalent per kWh given on the settings page. This is defaulted to the UK government-approved value.
Factory
Name (of factory/location)
Cost per kWh
Carbon Footprint per kWh
Machines
Name (of machine (s))
Number of phases
Voltage
Power Factor
General
Currency (e.g. GBP)
Hourly rate
Monitoring energy usage rates means manufacturers can identify inefficiencies, equipment malfunctions, or process bottlenecks, and take action to mitigate them. This proactive approach not only helps save on energy costs but also enhances overall efficiency.
Energy monitoring, equally, plays an important role in promoting sustainability and environmental responsibility. By monitoring energy consumption, businesses can identify opportunities for energy savings, reduce their carbon footprint, and fulfil sustainability goals.
Energy monitoring empowers production managers with real-time data and insights, enabling them to identify inefficiencies, set consumption targets, and implement energy-saving measures.
- Identifying Energy Inefficiencies: Energy monitoring provides real-time data on energy consumption patterns and usage trends. By closely monitoring this data, production managers can identify areas where energy is being wasted or used inefficiently. This can include pinpointing equipment malfunctions, process bottlenecks, or unnecessary energy consumption during idle periods. By identifying these inefficiencies, managers can take corrective actions to optimise energy consumption rates.
- Setting Energy Consumption Targets: With energy monitoring data, production managers can establish realistic energy consumption targets for processes and production lines. Manufacturers can use these targets to identify deviations in actual energy usage and make necessary changes to bring consumption back in line with the targets. This approach ensures that consumption rates are optimised to meet operational requirements.
- Implementing Energy-Saving Measures: By analysing consumption patterns, managers can identify opportunities for equipment upgrades, process optimisations, or changes in operational procedures to reduce energy consumption. These measures can include using more energy-efficient equipment, implementing automation systems, or optimising production schedules to minimise energy waste.
Ready to
Learn More?
See how FourJaw's plug-and-play analytics can help you turn machine data into real productivity gains. What would you like to do next?
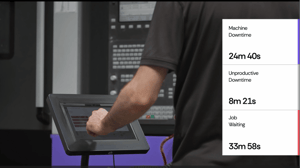