The history of Scrum dates back to the early 1980s when it emerged as a response to the challenges faced in traditional project management approaches.
Over the years, Scrum gained widespread adoption beyond software development, spanning manufacturing, healthcare, education, and marketing industries.
This article looks at how, by applying the principles of Scrum alongside lean manufacturing, companies can achieve greater agility, efficiency, and responsiveness in their production processes, ultimately leading to improved quality, reduced lead times, and increased customer satisfaction.
A brief history of Scrum
Scrum was initially introduced by Hirotaka Takeuchi and Ikujiro Nonaka in a Harvard Business Review article titled "The New New Product Development Game" in 1986. Takeuchi and Nonaka studied successful product development practices at companies like Honda, Fuji-Xerox, and Canon. They identified a pattern of iterative, cross-functional teamwork that they likened to forming a rugby scrum.
In the early 1990s, Jeff Sutherland, along with Ken Schwaber and Mike Beedle, further developed and formalised the Scrum framework. They codified Scrum's principles and practices, drawing inspiration from various sources including Lean manufacturing, empirical process control theory, and Agile software development methodologies.
Scrum gained popularity in the software development industry during the late 1990s and early 2000s as organisations sought more adaptive and flexible approaches to managing complex projects. Schwaber and Sutherland co-authored the Agile Manifesto in 2001, which outlined principles for Agile software development, with Scrum being one of the prominent Agile frameworks.
Scrum has continued to evolve and adapt to meet the changing needs of modern organisations. Variations and extensions of Scrum, such as Scrum@Scale, Nexus, and Large Scale Scrum (LeSS), have been developed to address the complexities of scaling Scrum across large enterprises and complex projects.
Today, Scrum is one of the most widely used Agile frameworks, with millions of practitioners worldwide. Its principles and practices have transcended the realm of software development and continue to shape the way organisations approach project management, product development, and teamwork.
Scrum and Lean Manufacturing. How they work together
Scrum has been successfully used in manufacturing and works effectively alongside lean manufacturing principles. Here's how:
Waste Elimination: Both Scrum and Lean focus on identifying and eliminating waste in processes. Lean manufacturing techniques such as value stream mapping can be used to identify areas of waste in manufacturing processes.
Scrum's iterative approach allows teams to continuously identify and address waste in their work, leading to incremental improvements over time.
Continuous Improvement: Scrum and Lean both emphasise the importance of continuous improvement. In Lean manufacturing, this is achieved through practices like kaizen, which involves small, incremental changes to improve processes.
Scrum's regular retrospectives provide a structured mechanism for teams to reflect on their performance, identify areas for improvement, and implement changes in subsequent iterations.
Customer Focus: Both Scrum and Lean place a strong emphasis on delivering value to the customer. Lean manufacturing principles such as customer pull and just-in-time production ensure that products are produced efficiently to meet customer demand.
Scrum's iterative development approach allows teams to prioritise features based on customer feedback and deliver valuable increments of the product at the end of each sprint.
Visual Management: Visual management techniques, such as Kanban boards, are commonly used in both Scrum and Lean manufacturing to make work visible and track progress.
Kanban boards can be used to visualise the flow of work through the manufacturing process and identify bottlenecks or areas of inefficiency. In Scrum, Kanban boards are often used to visualise the progress of tasks during sprints and ensure that work is completed on time.
Cross-Functional Teams: Scrum promotes the use of cross-functional teams with members from different disciplines working together towards a common goal. Similarly, Lean manufacturing encourages the formation of cross-functional teams to improve communication, collaboration, and problem-solving.
By leveraging the diverse skills and perspectives of team members, both Scrum and Lean can drive innovation and improve outcomes.
Scrum Example In Automotive Manufacturing
In automotive manufacturing, the production of a new car model can involve numerous teams working on different components such as bodywork, engine assembly, interior features, and electronics. To streamline the production process and ensure the timely delivery of high-quality vehicles, some automotive manufacturers have adopted Scrum principles.
Cross-functional Teams: The automotive manufacturer forms cross-functional teams consisting of engineers, designers, production workers, quality assurance specialists, and supply chain managers. Each team is responsible for a specific aspect of the car's production.
Sprints: The production process is divided into sprints, typically lasting one to four weeks, during which teams focus on completing specific tasks or milestones. For example, one sprint might focus on designing and testing a new dashboard layout, while another might involve optimising the engine assembly process.
Daily Stand-ups: Each day, teams hold brief stand-up meetings to discuss progress, identify any obstacles, and plan their tasks for the day. These meetings ensure that everyone is aligned on goals and priorities and that any issues can be addressed promptly.
Continuous Improvement: At the end of each sprint, teams conduct retrospectives to reflect on what went well, what didn't, and how they can improve. For instance, the team responsible for bodywork might identify a more efficient welding technique, while the interior design team might find ways to reduce material waste.
Scrum is often used by automotive manufacturers to improve efficiency and remove defects from the production line.
Visual Management: Visual management techniques such as Kanban boards are used to track the progress of tasks and ensure that production flows smoothly. Teams can easily see which tasks are in progress, which are completed, and which are pending, allowing for better coordination and transparency.
By applying Scrum principles in automotive manufacturing, companies can achieve several benefits:
-
Faster time-to-market for new car models.
-
Improved collaboration and communication between teams.
-
Better adaptability to changes in customer preferences or market conditions.
-
Higher product quality due to continuous feedback and improvement.
Overall, this example demonstrates how Scrum principles can be successfully adapted and applied in manufacturing settings to optimise production processes and drive business success.
Implementing the Scrum framework in a manufacturing environment
As with most things worth doing, careful planning and consideration must happen before implementing a Scrum framework within a manufacturing process. Here are some top tips and considerations for manufacturers before implementing Scrum:
Understand Scrum Principles: Ensure that key stakeholders, including leadership and team members, have a clear understanding of Scrum principles, values, and practices. Education and training may be necessary to familiarise everyone with the framework and its benefits. If you're looking for a good book that explains the principles behind scrum, we recommend 'Scrum The Art of Doing Twice The Work In Half the Time'.
Assess Organisational Readiness: Evaluate the organisation's culture, structure, and readiness for adopting Scrum. Consider factors such as existing processes, hierarchies, and attitudes towards change. It's important to have buy-in from all levels of the organisation to implement Scrum successfully.
Identify Suitable Projects or Processes: Select pilot projects or processes that are well-suited for Scrum implementation. Look for projects with clear goals, cross-functional teams, and opportunities for iterative development and improvement. Start with smaller, less complex projects to gain experience and demonstrate success.
Form Cross-Functional Teams: Establish cross-functional teams with members from different departments or areas of expertise. Ensure that teams are self-organising and empowered to make decisions autonomously. Encourage collaboration, communication, and a shared sense of accountability among team members.
Define Clear Goals and Metrics: Set clear goals, objectives, and manufacturing-based metrics for Scrum implementation. Define what success looks like and how it will be measured, whether it's increased productivity, faster time-to-market, improved quality, or higher customer satisfaction. Regularly review and adjust goals based on feedback and progress.
Adapt Scrum Practices to Manufacturing: While Scrum was originally designed for software development, it can be adapted to fit manufacturing processes. Tailor Scrum practices such as sprint planning, daily stand-ups, sprint reviews, and retrospectives to suit the specific needs and requirements of manufacturing projects.
Invest in Tools and Infrastructure: Provide the necessary tools, resources, and infrastructure to support Scrum implementation. This may include project management software, visual management tools, physical or digital Kanban boards, and manufacturing analytics software, such as machine monitoring and communication platforms for remote teams. Ensure that teams have access to the tools they need to collaborate effectively and track progress.
Promote Continuous Improvement: Foster a culture of continuous improvement and learning within the organisation. Encourage teams to experiment, innovate, and adapt their processes based on feedback and results. Conduct regular retrospectives to reflect on what's working well, what could be improved, and how to make adjustments moving forward.
Provide Leadership and Support: Leadership support is crucial for the success of Scrum implementation. Leaders should champion the adoption of Scrum, provide guidance and resources, and remove any obstacles or barriers that hinder progress. Lead by example and demonstrate a commitment to the principles and values of Scrum.
Be Patient and Persistent: Implementing Scrum is a journey that requires time, effort, and patience. Be prepared for challenges, setbacks, and resistance to change along the way. Stay committed to the process, learn from mistakes, and celebrate successes as you gradually transform the organisation's approach to manufacturing.
Understand the differences between Lean manufacturing and Scrum
Lean manufacturing and Scrum are related concepts but not the same thing. They both aim to improve processes and increase efficiency, but they approach it from different angles and have distinct methodologies.
Lean Manufacturing:
Lean manufacturing, often associated with the Toyota Production System, focuses on eliminating waste and maximising value for the customer.
It emphasises principles such as continuous improvement (kaizen), just-in-time production, and respect for people.
Lean techniques include value stream mapping, 5S (Sort, Set in order, Shine, Standardise, Sustain), SMED (Single-Minute Exchange of Dies) Kanban systems, and Poka-yoke (error-proofing).
Image shows the seven steps of SMED: SMED is a method of lean manufacturing used for a quick, simplified, and efficient production set-up and changeover from one product or process to another, to reduce non-productive downtime and stoppages.
Lean aims to create a smooth, efficient flow of materials and information throughout the production process while minimising waste, such as overproduction, excess inventory, defects, waiting time, unnecessary transportation, and underutilised talent.
Scrum:
Scrum is a framework primarily used in software development, but more recently its principles have been applied in various industries, including manufacturing.
It is based on iterative and incremental development, with a focus on delivering high-quality products in short time frames called sprints.
Scrum teams are cross-functional and self-organising, and they work collaboratively to deliver potentially shippable increments of work at the end of each sprint.
Scrum includes practices such as daily stand-up meetings, sprint planning, sprint reviews, and retrospectives to facilitate communication, transparency, and continuous improvement.
While both lean manufacturing and Scrum aim to improve processes and deliver value efficiently, they differ in their approaches, tools, and focus areas. Lean manufacturing is more holistic and encompasses a broader range of principles and techniques, whereas Scrum is more specific to project management and iterative development.
Scrum, A final thought
Manufacturers can benefit from integrating principles from both lean manufacturing and Scrum to optimise their processes and achieve better results.
By applying the principles of Scrum to manufacturing, companies can achieve greater agility, efficiency, and responsiveness in their production processes, ultimately leading to improved quality, reduced lead times, and increased customer satisfaction.
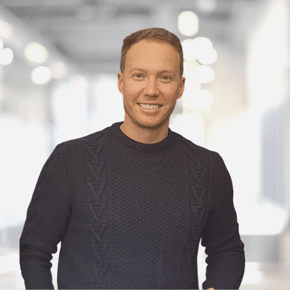