Manufacturing is a busy, ever-changing environment, companies are constantly seeking ways to improve efficiency, reduce waste, and enhance overall productivity. One highly effective approach gaining popularity is the implementation of the 5S methodology.
Introduction to the 5s Methodology
Originating from Japan, the 5S methodology is a systematic process with a series of identifiable steps, each building on its predecessor aimed at organising and optimising the workplace. The five key principles—Sort, Set in order, Shine, Standardise, and Sustain—create a foundation for a more streamlined and productive manufacturing environment.
This article defines each of the 5S, explores some of the key things to consider before implementing the 5S methodology, and if those are satisfied the benefits the 5S can bring to a manufacturing environment.
The phases of the 5S
Sort (Seiri):
The first step in the 5S methodology is to "Sort," which involves systematically identifying and removing unnecessary items from the factory floor. This step promotes a clutter-free environment and helps in identifying essential tools, equipment, and materials required for efficient operations. By decluttering the workspace, manufacturers can reduce the risk of errors, improve safety, and optimise the use of available space.
Set in Order (Seiton):
"Set in Order" focuses on arranging and organising the remaining items logically and efficiently. This step involves creating a designated place for each tool or material to ensure quick and easy access. Implementing visual cues, such as labels and colour-coded markings, can further enhance organisation. An organised workspace minimises the time spent searching for tools and materials, leading to increased productivity and reduced downtime.
An example of an organised workspace that uses labels and a form of shadow board to organise tooling.
Shine (Seiso):
The "Shine" step emphasises cleanliness and maintenance. Regular cleaning of work areas and equipment not only ensures a safe and healthy environment but also aids in identifying potential issues early on. Routine maintenance prevents the deterioration of machinery and equipment, thus helping to extend its lifespan. A clean and well-maintained workplace fosters a sense of pride among employees and contributes to positive work culture.
Standardise (Seiketsu):
"Standardise" involves developing and implementing standardised work processes and procedures. This step ensures consistency in operations, reduces variability and enhances overall efficiency. Standardisation also facilitates training and onboarding processes, as new employees can quickly understand and adapt to established practices. Regular audits and inspections help maintain the standardised processes over time.
Sustain (Shitsuke):
The final step, "Sustain", is about ensuring continuous adherence to the 5S principles. This involves creating a culture of continuous improvement and employee engagement. Regular training, ongoing monitoring, and incorporating 5S principles into performance evaluations help embed these practices into the organisational culture, from the factory floor to the top floor. Sustaining the 5S methodology ensures long-term benefits and a continuously improving manufacturing environment.
The 5S uses a series of identifiable steps, each building on its predecessor as shown in this simplified diagram.
Free Resource: 5S For a Lean Workplace Posters
Download our free 5S for a Lean Workplace posters and use them on the factory floor noticeboards to help ensure the 5S are top of mind, helping create a culture of continuous improvement.
Factors to consider before implementing the 5S:
Before implementing the 5S methodology in your manufacturing environment, it's important to consider several key factors to ensure a successful and sustainable integration. Here are some important things to consider:
Management Commitment:
- Leadership Support: Ensure that top management is fully committed to the 5S implementation. Like any company-wide initiative, ensuring leadership support is crucial for overcoming resistance to change and fostering a culture of continuous improvement.
Employee Involvement:
- Training and Communication: Provide comprehensive training to employees on the principles of 5S and the expected benefits. Effective communication is essential to garner employee support and engagement from the very start of the process and throughout.
Customisation to the Work Environment:
- Tailoring the Methodology: Every manufacturing environment is unique, it’s therefore important to acknowledge this and tailor the 5S methodology to suit the specific needs, processes, and challenges of your manufacturing environment. Simply taking a one-size-fits-all approach may not be as effective and could lead to some or all of the project falling short of its potential effectiveness.
Initial Assessment:
- Current State Analysis: Conduct a thorough assessment of the current state of each area of the factory floor. Identify areas of improvement, potential obstacles, and prioritise areas where the 5S methodology will have the most significant impact. For example, utilise any systems you have in place, such as machine monitoring, that can provide valuable insight into the current productivity of the factory floor, and start by focusing on areas where the largest proportion of unplanned machine downtime occurs.
Resource Allocation:
- Allocate Adequate Resources: Like any business initiative, the project must be given the best possible chance of success by providing the necessary resources, including time, manpower, and financial support, to facilitate the successful implementation of 5S. Lack of resources can hinder progress, cause frustration among those leading the initiative and undermine the effectiveness of the methodology.
Realistic Goals and Metrics:
- Establish Measurable Objectives: Set realistic and measurable goals for the 5S implementation. Define key performance indicators (KPIs) and use the right manufacturing metrics for your business to track progress and evaluate the success of the initiative.
Continuous Improvement Mindset:
- Encourage Continuous Learning: Instill a mindset of continuous improvement. Recognise that 5S is not a one-time project but an ongoing process. To help embed this mindset, it’s valuable to follow Kaizen principles that allow you to establish mechanisms for feedback, and regularly review and refine the implementation strategy.
Overcoming Resistance:
- Addressing Resistance: Change can be uncomfortable for some people. The best way to deal with this is to try to anticipate and address resistance from employees who may be sceptical or uncomfortable with change. Well-thought-through communication explaining the benefits and how it will make their lives easier is a proven method to overcome resistance. As we mentioned earlier, where possible, try to involve employees in decision-making or as early as possible in the process to foster a sense of ownership.
Integration with Existing Systems:
- Align with Existing Processes: Ensure that the 5S methodology aligns with existing production processes and quality management systems. Integration with other improvement initiatives will enhance the overall effectiveness and help you track progress against the KPIs you put in place.
Cultural Considerations:
- Respect Organisational Culture: Recognise and respect the existing workplace culture. Align the 5S implementation with the values and norms of the organisation to facilitate smoother acceptance by employees. Remember, no two manufacturers are the same!
By carefully considering each of these factors against your manufacturing business before setting out to implement the 5S methodology, you can set the stage for a successful and sustainable transformation that brings about positive changes in efficiency, organisation, and overall workplace culture.
Benefits of Implementing the 5S Methodology
The 5S methodology yields a multitude of benefits for manufacturing environments. By systematically incorporating the principles of Sort, Set in Order, Shine, Standardise, and Sustain, manufacturers experience enhanced efficiency, improved safety, and increased productivity. Here’s a summary of these benefits.
- Improved Efficiency: The 5S methodology optimises workflows, reduces unproductive downtime, and enhances overall operational efficiency.
- Enhanced Safety: A well-organised and clean workplace minimises safety hazards, reducing the risk of unforeseen incidents, accidents and injuries.
- Increased Productivity: By reducing the time wasted on the top causes of machine downtime, such as searching for tools and materials, machine operators can focus on productive tasks, leading to increased output.
- Cost Reduction: The elimination of unnecessary items, processes, production bottlenecks, and preventive maintenance contributes to cost savings by lowering the cost of manufacturing goods. Enabling manufacturers to make more products with the same resources at a lower cost.
- Quality Improvement: Standardising production processes and operating within a clean workspace contribute to improved product quality and reduced defects.
- Employee Engagement: Involving employees in the 5S implementation process fosters a sense of ownership and pride in their workplace. Improving employee engagement also leads to higher staff retention rates and improved collaboration among team members and peers.
- Flexibility and Adaptability: We started this article by acknowledging that manufacturing doesn’t stand still. Macro and Micro factors continually change. Therefore, operating an organised and standardised manufacturing environment allows for easier adaptation to changes in wider economic events as well as internal production requirements and processes.
Conclusion: Implementing the 5S Methodology in Manufacturing:
Implementing the 5S methodology in a manufacturing environment is a strategic investment that yields long-term benefits. By systematically applying the principles of Sort, Set in Order, Shine, Standardise, and Sustain, companies can create a workplace that is not only more efficient and organised but also safer, more cost-effective, and conducive to continuous improvement.
As manufacturing continues to evolve, the 5S methodology remains a valuable tool for companies seeking to thrive in a competitive and dynamic industry. Overall, the 5S methodology stands as a comprehensive approach that not only transforms the physical workspace but also cultivates a culture of continuous improvement, positioning manufacturing entities for sustained success.
FourJaw's machine monitoring software supports the successful implementation and continuous use of the 5S methodology within manufacturing. Book a demo via the form below to find out how.
Book a Demo of FourJaw
Request a demo today and discover how FourJaw's IoT platform can help transform your manufacturing operations, saving valuable resources and strengthening your bottom line.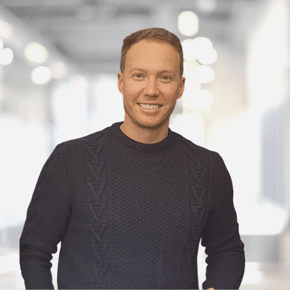