Tracking machine downtime is one of the simplest and most effective ways to make sure assets on the factory floor are being used efficiently, but this hasn’t always been true.
Historically, capturing machine data has relied on manual data capture processes or solutions that have been out of reach for many manufacturers due to the large upfront costs and complicated system integration requirements.
Today, thanks to advances in technology, automated machine downtime tracking is more accessible and affordable than ever. Providing insights that enable stakeholders across entire factory operations to become more efficient, competitive, sustainable and ultimately more profitable.
This article looks at real-life examples of how manufacturers use automated machine downtime tracking to drive efficiency across their factory floors. We start by defining machine downtime tracking, and then provide the use cases, business impact and finish by providing some key takeaways.
What is machine downtime tracking?
Machine downtime tracking in manufacturing refers to the systematic recording and analysis of the periods during which manufacturing equipment is not operational or not producing goods as expected. This involves monitoring and documenting instances when machinery is idle due to unplanned or planned downtime, such as failures, maintenance, adjustments, or any other interruptions.
The key objectives of machine downtime tracking include:
Identifying Root Cause: Determining the reasons (root cause) for downtime, whether they are due to mechanical failures, operator errors, maintenance activities, or other factors.
Measuring Duration: Recording the length of time the machinery is non-operational to understand the impact of unplanned and planned downtime on production schedules.
Improving Efficiency: Analysing downtime data to identify patterns, improve maintenance schedules, optimise operational processes, and ultimately reduce the frequency and duration of downtime.
Enhancing Productivity: Ensuring that machinery operates at optimal levels to maximise production output and efficiency.
Cost Management: Reducing the financial impact associated with downtime by implementing effective strategies and solutions based on the tracked data.
Overall, machine downtime tracking is an essential practice in manufacturing that helps maintain operational efficiency, enhance productivity, and minimise costs associated with unexpected machine stoppages.
WATCH: Precision Machining Manufacturer Achieves 25% Machine Utilisation Uplift
The impact of Machine Downtime if left unmanaged
Manufacturers know they’re only earning when their machines are running, and most manufacturers now recognise that technology offers the best route to keep those machines running and deliver greater productivity.
If machine downtime isn't tracked correctly across a manufacturing process, it can negatively affect several areas, including:
Reduced Productivity: Without accurate downtime tracking, it becomes difficult to understand the true extent of production losses. This can lead to a significant reduction in overall productivity as unidentified production issues persist.
Increased Operational Costs: Downtime that isn't properly monitored can result in unplanned and frequent stoppages, leading to increased costs due to lost production time, overtime labour, expedited shipping, and other expenses.
Poor Maintenance Management: Ineffective asset tracking prevents the identification of recurring issues, which hampers the development of a proactive maintenance strategy. This can result in more frequent and severe equipment failures, resulting in production bottlenecks and longer product lead times.
Lower Product Quality: Inconsistent operation and sudden stoppages can affect the quality of the products being manufactured, especially within process manufacturing lines. This can lead to higher rejection rates and increased rework or scrap.
Missed Delivery Deadlines: Untracked downtime can cause delays in production schedules, leading to missed delivery deadlines and potentially damaging relationships with customers.
Inefficient Resource Allocation: If downtime isn't accurately recorded and analysed, resources such as labour and materials may not be allocated efficiently, leading to wastage and suboptimal use of assets. Having a direct impact on working capital, as well as production and planning.
Poor Decision-Making: Management relies on accurate data to make informed decisions. Inaccurate downtime tracking leads to poor insights, which can result in misguided strategic decisions affecting the entire manufacturing process. Even if you’re doing manual machine downtime tracking, it will be prone to human errors, will likely be outdated by the time you review the data and can lead to decisions made on opinion rather than fact.
Competitive Disadvantage: Companies that do not track downtime effectively may find themselves at a competitive disadvantage compared to those that use accurate and real-time data to optimise their operations and reduce inefficiencies. This may affect competitiveness relating to meeting demand, due to capacity constraints, reputational damage due to delivering products late, and not being competitive on price due to inaccurate quoting.
Read the case study to find out how they saved more than 270 lost productive hours per week due to machine downtime.
The benefits of Automated Machine Downtime Tracking.
Whether making parts for an aircraft or crisps for consumers, manufacturers of all sizes, across all sectors are increasingly adopting technology to see what’s happening in their factories and using data to optimise processes and decision-making.
We see production issues solved faster thanks to better communication, better investment decisions based on an objective assessment of needs, and data sharing across departments to invite new ideas and inspire continuous improvement.
Earlier this year, we interviewed a cross-section of manufacturers who have all deployed digital technologies to enable them to track their machine downtime. Here’s what they had to say:
Increasing Machine Uptime
“We’re hugely data-driven now. It’s one of the big changes over the last couple of years. We’re able to very quickly go from data to insights that people can then take action from, which is a massive benefit to us,” says Sean Thomas at AVPE Systems. “We look at the output and analyse it daily to identify different causes of downtime and areas of concern that we need to act upon immediately.”
“We used to see that people would focus on trying to fix the things that were the most irritating for them rather than necessarily the things causing the most downtime or the most lost productivity. So it’s put us much more in control of the impact of those changes and making sure that we can start the projects that will have the biggest impact the quickest,” adds Thomas.
“Since we started using data to target our improvement activities, we’ve seen roughly a 30% increase in uptime on the shop floor.”
Removing Production Bottlenecks in real-time
“We use systems that give us real-time utilisation data on our machines. If, for any reason, we see that those machines are not performing the way we’d want them to meet our output targets, we can then find out the reason for that and make corrective changes and actions on the shop floor,” says Armac Martin’s Steven West. “Relieving pressure points is a good way to describe it.
With our data, we can see where the pressure points are, and that’s where we can focus to ensure we relieve those.”
Informed Decision Making
“It’s very easy to assume why a machine is not running, and the reality is generally very different,” adds Stuart Cook from Hydrafeed. “We all have good people that work for us. We want to help them and understand the challenges that they’re having, and having the visibility of the reasons why they’re not able to continue doing their job is priceless for us to be able to look at that and then start to work with them to tackle those issues and reduce that downtime.”
We use a lot of data in planning, which has got a lot of assumptions in it in terms of how productive different areas of the facility will be,” he adds. “[Machine monitoring data] allows us to compare assumptions made at the planning stage to our actual execution at the end, which means that we can look at the gaps and where we can best fill those gaps to make those planning assumptions come true.
Over time, we’ve improved those planning assumptions and ensure we’re not over-committing to customers or underutilising resources.” “Our data-driven insights have enabled us to increase output through a period of exponential growth. We’ve had to upscale our operations to meet customer demand,” reveals Steven West, Armac Martin.
Get access to our report ‘Digital Excellence In Manufacturing’ to hear more from manufacturers sharing their experience of using digital technologies to achieve manufacturing excellence on their factory floor.
Machine Downtime Tracking - Key Takeaways:
Data-Driven Decision-Making: Accurate data and analytics are fundamental in driving productivity on the shop floor. Manufacturers leverage real-time data insights to identify causes of downtime, improve operational efficiency, and effectively target improvement activities. Manufacturers can make informed decisions to optimise processes and relieve bottlenecks by analysing machine utilisation data and identifying pressure points, resulting in increased uptime and improved productivity.
Enhanced Planning and Processes: Data-driven insights transform planning processes by consolidating data from various sources and formats to create a digital version of the factory. This digital representation enables manufacturers to predict outcomes, assess the impact of urgent customer requirements, and adjust planning assumptions accordingly. By comparing planning assumptions to actual execution, manufacturers can optimise resource utilisation, minimise gaps, and meet customer demand more efficiently.
Informed Asset Investment Decisions: Data-driven insights support asset investment decisions by providing an accurate view of what is happening on the factory floor. By understanding the cost-effectiveness of automation and robotics compared to human labour, manufacturers can prioritise investments based on tangible benefits and ROI.
If you're struggling with production challenges on your factory floor, reach out to our team via the form below, to find out how we can help you remove costly machine downtime, to improve your operational efficiency.
Start Tracking Machine Downtime in your Factory
Book a personalised product demonstration and find out how easy it is to track machine downtime in your factory.
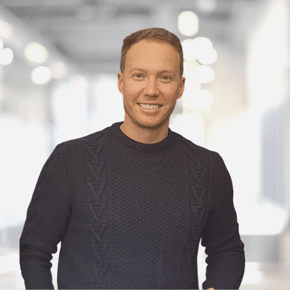