When it comes to implementing new digital tools or processes within a manufacturing environment, it is impossible to overstate how important and influential culture is to ensure it is adopted successfully across the organisation. It takes a well-structured, thought-through culture of innovation and willingness to improve if the new technology is ever going to become part of the furniture.
We have taken the opportunity to speak with some of our customers who are forward-thinking manufacturers from across the country of all shapes and sizes to uncover their best advice for successfully implementing digital tools and driving process improvements on the factory floor. In the article below, we share their top tips.
PILOT AND SCALE
Start small, test the tools in a controlled environment, and scale gradually.
Why it matters: Piloting reduces risk and allows you to refine processes before rolling out changes across the entire factory floor.
Expert tip: Choose a pilot project that is impactful yet manageable and evaluate its performance before scaling. Use lessons learned to guide broader implementation.
LEADERSHIP
Ensure leadership is actively engaged and supportive of the digital transformation process.
Why it matters: Visible commitment from leaders fosters trust and sets a positive tone for the initiative.
Expert tip: Leadership should communicate the “why” behind the changes, regularly check in with teams, and address challenges openly to maintain momentum.
Targets
Ensure you have measurable targets with a clean start and end state and actively track progress.
Why it matters: Clear targets create a roadmap for implementation and help keep everyone focused on shared objectives.
Expert tip: Break down large targets into smaller, incremental goals that can be regularly reviewed and adjusted if needed. This keeps the momentum going and ensures alignment at all levels.
Metrics
Any change or transformation programme must have well-defined metrics so the people involved know if the initiative has been a success or not.
Key manufacturing metrics to consider: Machine uptime, production efficiency, OEE, scrap rates, and lead times.
Expert tip: Engage your team in identifying these metrics early in the process, ensuring they’re realistic and directly linked to business goals.
Training
Equip your team with the knowledge and skills to use the new tools effectively.
Why it matters: A lack of understanding or confidence can slow adoption and reduce the effectiveness of digital tools.
Expert tip: Offer hands-on training (virtual or in-person) sessions tailored to different roles and create easy-to-access resources like user guides or video tutorials. Ensure you choose a partner that is willing to provide ongoing support to address questions as they arise.
Impact
It’s important to understand that any change or transformation initiative needs to have a tangible positive impact on the daily lives of staff.
How to ensure impact: Involve your workforce in the planning and implementation phases to gather feedback and address concerns.
Expert tip: Use real-life examples to show how similar tools have improved workflows, reduced manual tasks, or enhanced safety.
Measure
When implementing new processes or tools, proactively measure the ROI or business impact to ensure the expected improvements are being achieved.
What to measure: Cost savings, increased throughput, reduced downtime, or improved product quality.
Expert tip: Regularly share results with your team to maintain transparency and highlight the value of their efforts.
COMMUNICATION
Keep everyone informed and aligned throughout the implementation journey.
Why it matters: Poor communication can lead to resistance, confusion, and missed opportunities.
Expert tip: Use clear, consistent messaging across multiple channels—such as team meetings, dashboards and emails, and daily stand-ups - such as Kaizen events — and invite feedback to ensure all voices are heard.
Celebrate
Celebrate improvements openly across the business and acknowledge the team effort it takes to implement digital tools successfully to have a benefit on the factory floor.
Why it matters: Recognition boosts morale, reinforces a culture of continuous improvement, and encourages buy-in for future initiatives.
Expert tip: Host a team event, share success stories on internal platforms, or give shoutouts to individuals who went above and beyond.
FEEDBACK LOOP
Create a system to gather continuous feedback and adjust the implementation as needed.
Why it matters: Regular feedback ensures that the tools remain effective and that any issues are promptly addressed.
Expert tip: Establish regular check-ins or surveys to collect input from frontline/ factory floor staff, and involve them in brainstorming solutions.
We hope you found this article helpful and it has provided you with some practical takeaways that you can use if you're embarking on a digital transformation project within your business. Please feel free to check out further resources in our learning library.
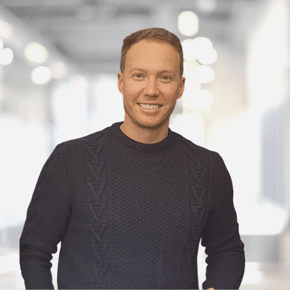