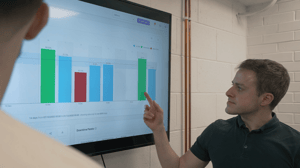
Key Manufacturing Metrics
Understand THE KEY MANUFACTURING METRICS AND THE ONES THAT ARE RIGHT FOR YOUR BUSINESS
Defining Key Manufacturing Metrics
Manufacturing metrics are quantifiable measurements used to assess various aspects of the manufacturing process and performance.
These metrics provide objective and data-driven insights into the efficiency, quality, productivity, and overall effectiveness of manufacturing operations. By tracking and analysing these metrics, organisations can identify areas for improvement, make informed decisions, and drive continuous optimisation in their manufacturing processes.
Manufacturing metrics help stakeholders understand how well the production process is performing and whether that performance aligns with the organisation's goals and objectives.
Key Manufacturing Metrics:
At the heart of any successful manufacturing operation lies the ability to understand and optimise a diverse set of key performance indicators. Manufacturers must carefully select and track relevant metrics based on the unique needs of their specific industry sector.
Each manufacturing subsector faces distinct challenges, and choosing the right metrics to track can guide improvements that significantly impact performance and profitability.
There are five key manufacturing metrics that we come across often with our clients. These are:
- Overall Equipment Effectiveness (OEE)
- Downtime
- Utilisation
- Total Effective Equipment Performance (TEEP)
- First Pass Yield (FPY)
Let’s look at each of these in more detail.
Overall Equipment Effectiveness
Overall Equipment Effectiveness, or OEE, is used in manufacturing to measure a machine's productivity. It’s a metric primarily used for large-volume, production-line manufacturing. An OEE report gives factory managers reliable information used to maximise output and improve performance.
OEE is a crucial metric that calculates the effectiveness of manufacturing equipment by taking into account three components: Availability, Performance, and Quality. Primarily in large volume, production line manufacturing, OEE provides insights into how well equipment is utilised, how often it operates at its full potential, and the rate of production of good-quality products.
By identifying inefficiencies in equipment utilisation and performance, manufacturers can optimise production processes and improve overall productivity.
Learn more about what OEE is and how to improve OEE in our helpful guides. You can also monitor your OEE in real-time with our OEE machine monitoring software.
Machine Downtime
Machine downtime refers to periods when a machine is unavailable for production. There are two types of machine downtime: planned (productive) downtime, and unplanned (unproductive) downtime. This metric is ideal for all types of manufacturers, including batch, process/high volume.
Reducing unplanned downtime is essential to minimise production delays, increase output, and reduce costs.
By analysing downtime data, manufacturers can identify root causes of equipment breakdowns and implement preventive maintenance measures, leading to improved operational efficiency and higher profitability.
Learn why understanding machine downtime is so important, and see how FourJaw’s machine downtime monitoring software can help boost productivity and reduce costs.
Machine Utilisation
Machine Utilisation measures the percentage of time that equipment is in use during planned production hours, enabling businesses to optimise production capacity and reduce lead times. Similar to machine downtime, utilisation is also a suitable manufacturing metric for a range of manufacturing types.
Low machine utilisation rates indicate potential bottlenecks or underutilisation of resources. By optimising equipment utilisation, manufacturers can maximise production capacity, reduce lead times, and enhance overall productivity.
Total Effective Equipment Performance (TEEP)
Often used in large-volume manufacturing, TEEP combines OEE and utilisation metrics to provide a comprehensive assessment of equipment performance. It measures the overall efficiency of equipment by considering both planned and unplanned downtime
TEEP helps manufacturers identify losses caused by factors such as equipment breakdowns, changeovers, and other non-productive events. By analysing TEEP data, manufacturers can make informed decisions to improve equipment efficiency and reduce operational costs.
First Pass Yield (FPY)
First Pass Yield (FPY) is also known as Throughput Yield (TPY) and is the percentage of products that pass quality inspection on the first attempt (right first time). FPY/TPY is a metric used often in large volume, production line manufacturing.
High FPY indicates that the manufacturing process is consistently producing products of the desired quality. By monitoring FPY, manufacturers can identify areas for improvement in their processes, reduce waste, and enhance customer satisfaction with defect-free products.
While these five metrics are common in manufacturing, they by no means constitute an exhaustive list. Below, we’ve included some more manufacturing metrics that may be more relevant to your manufacturing operations.
Productivity Metrics
Capacity Utilisation
Refers to how much of a plant's total capacity is in use.
The rate of capacity utilisation equals the ratio of the actual output over the maximum potential output multiplied by a hundred per cent.
Cycle Time
Cycle time measures the time it takes to complete a single production cycle. It's a critical metric for understanding production efficiency and identifying bottlenecks that might be causing delays. Cycle time refers to the average time between the completion of units; to calculate it, divide the number of units by the time taken to complete them. For example, If 80 units are completed in a 40-hour week, the cycle time is 2 hours on average.
On-Time Delivery
The percentage of products delivered on time compared with the total quantity of products delivered. To calculate on-time delivery, divide your total number of on-time deliveries by your total number of deliveries, then multiply your result by 100 to get a percentage.
Recovered Hours
A metric used to measure the performance of an asset over a time period. It is calculated by multiplying the cycle time by the number of units produced. However, it is often open to error due to incorrect base data on cycle time or because setups/productive downtimes are not accounted for as part of the measure.
Customer Order Fill Rate
This metric indicates the percentage of customer orders that are filled on time and in full. It reflects the company's ability to meet customer demand accurately. Fill rate is the ratio of the number of orders fulfilled over the total number of orders received multiplied by the percentage.
Downtime
Downtime measures the amount of time that equipment or processes are not operational. Reducing machine downtime is crucial for maximising productivity.
Learn more about why understanding machine downtime is essential for manufacturers.
Production Volume
Measures how many units are made in a given timeframe. To calculate production volume, divide the standard direct labour hours of actual production by the budgeted direct labour hours, then multiply the answer by 100 to get a percentage.
TEEP
Combines OEE and utilisation metrics to provide a comprehensive assessment of equipment performance. The formula for calculating TEEP is: Performance x Quality x Availability (where Availability = Actual Production Time / All Time).
Quality Metrics
FTY
First Time Yield describes the ratio of the number of non-defective products released to the total number of units manufactured. To calculate FTY, divide the number of products that pass through a step of the process without error on the first attempt by the total number of products being tested.
MTBF
Mean Time Between Failures measures the reliability of equipment and how long it can operate before experiencing a failure. To calculate MTBF, divide the total uptime by the number of breakdowns that occurred over the same period.
Yield
Yield measures the percentage of products that meet quality standards out of the total produced. Tracking yield helps identify defects, quality issues, and potential areas for process improvement. To calculate the yield rate, simply divide the number of acceptable units by the total number of units entering production.
FPY
First Pass Yield (sometimes referred to as Throughput Yield (TPY)) is the percentage of products that pass quality inspection on the first attempt (right first time). It highlights the effectiveness of the production process and reduces the need for rework or additional processing. To calculate first pass yield, divide the acceptable parts by the total number of parts produced during manufacturing. The higher the calculation, the better your product overall. The formula for FPY is: FPY = Quality Units / Total Units Produced.
Scrap and Rework Rates
These metrics quantify the amount of materials discarded due to defects or the need for rework. Reducing scrap and rework rates improves resource utilisation, provides a higher margin, enables better capacity planning and lowers costs to free up working capital.
Customer Reject Rate
A measure of how many parts delivered to customers are defective, customer reject rate gives a good insight into the quality of your operations. To calculate reject rate, divide the number of rejected products by the total output.
Financial Metrics
Maintenance costs
All expenses required to maintain and repair equipment. When calculating total maintenance costs, you’ll need to take into account all components that are part of daily maintenance work, including labour costs, material parts price, and other invoices.
ROA
Return on Assets works out a manufacturer's profitability in relation to its available assets, dividing net income by the average value of total assets. To calculate ROA, divide a firm’s net income by the average of its total assets, then multiply it by 100 to get a percentage.
ROR
Rate of return is a percentage that accounts for the profit and loss resulting from an investment over time. To calculate the rate of return for an investment, subtract the value of the investment from its final value; then, divide this amount by the starting value of the investment, and multiply this figure by 100 to get a percentage.
Unit Costs
The average cost to manufacture one unit, taking into account both variable and fixed costs. To calculate unit costs. Combine your variable and fixed costs and divide this figure by the number of units produced.
Scrap Material Value
The amount manufacturers earn from their scrap material minus disposal costs. Selling scrap material is a good way for manufacturers to get a bit of extra money. Scrap material prices will vary depending on quality and the state of the current market; once you’ve determined a price, simply subtract your disposal costs to reveal scrap material value.
Inventory Turnover
Inventory turnover measures how many times inventory is used and replenished within a specific period. High turnover rates indicate efficient inventory management and reduced carrying costs. To calculate inventory turnover, divide the cost of goods sold by your average inventory value.
Implementing Manufacturing Metrics Successfully
Effective implementation of manufacturing metrics requires a data-driven culture within the organisation. Encouraging employees to embrace technologies that enable accurate, real-time data collection to inform decisions based on insights fosters a proactive approach to problem-solving and continuous improvement. By investing in smart technologies such as machine monitoring, manufacturers can effectively capture key production data and use it to make short, medium and long-term operational and commercial decisions.
To continuously improve performance, manufacturers must regularly review their KPIs to ensure they are the right metrics to be measuring based on the overall business goals. By remaining relevant and aligned with ever-changing business goals and market dynamics, manufacturers can unlock their full potential for growth, efficiency, and competitive advantage.
BEST PRACTICES
Set Achievable and Realistic Targets
Ensure the metrics you choose align with the organisation's overall KP’s/goals. Targets should be realistic and attainable, motivating teams to strive for continuous improvement without feeling overwhelmed by unattainable expectations.
Understanding benchmarks based on historical internal data and external industry data helps in evaluating performance accurately and identifying areas that need improvement.
Regularly Monitor and Analyse Data
Manufacturers should establish a regular data collection and analysis schedule, ensuring that insights are acted upon promptly.
Real-time monitoring using tools such as manufacturing analytics software enables manufacturers to make timely decisions and respond swiftly to emerging issues. Additionally, historical data analysis helps identify trends, patterns, and recurring challenges, allowing businesses to adopt preventive measures and make data-driven decisions that improve a process.
Invest in Employee Training
Training programs should focus on enhancing employees' data analysis and problem-solving skills, ensuring that they can interpret metric insights accurately and apply them effectively. A well-trained workforce is better equipped to identify the root causes of issues, collaborate on improvement initiatives, and contribute to achieving organisational goals.
Adapt Your Measures to Changing Market and Business Needs
If we can be certain of anything in the world of manufacturing, it’s safe to say it doesn’t stand still. As market dynamics change and new challenges arise, manufacturers should review and update their selected metrics to remain aligned with overarching business KPIs and goals. Flexibility in metric selection allows manufacturers to respond effectively to emerging trends and challenges, ensuring that you continue to provide relevant and valuable insights.
Involve Relevant Stakeholders
Engage employees at all levels, from the factory floor to top management. Involvement creates a sense of ownership and fosters a culture where employees understand the importance of the metrics being measured and how they contribute to the organisation’s overall KPIs.
An efficient way to make sure all stakeholders are aware of the key metrics being measured is by visualising the data on the factory floor using screens.
Implement Continuous Improvement Initiatives
By default, measuring key metrics in your manufacturing operations gives you the opportunity to continually improve based on the data being measured. By measuring, understanding and benchmarking your data enables you to remove inefficiencies that otherwise may have gone unnoticed. Implementing Kaizen methodologies will enable stakeholders at all levels to have a continuous improvement mindset.
Read our guide ‘How to implement a continuous improvement strategy’ in your factory.
Promote Knowledge Sharing
As we touched on earlier, getting staff at all levels to understand what and why you measure what you do within your processes ensures individuals, teams and the whole organisation can work to the best of their ability to achieve the overarching business goals.
Factory or team leaders should encourage a culture of internal knowledge sharing amongst their peers. For example, comparing machine utilisation data by shift or site is a great way to understand what has or is working well. Teams or individuals can then transfer that knowledge and apply it to processes that may not be working as well in their shift or site.
Real-Life Examples BY SUB-SECTOR
In the aerospace and defence industry, it is common for manufacturers to closely monitor the Mean Time Between Failures (MTBF) metric, which measures the reliability of equipment and how long it can operate before experiencing a failure. Additionally, the First Pass Yield (FPY) metric is essential in ensuring that the manufacturing process produces products meeting the required quality standards without the need for rework or repair during the first production attempt.
By tracking these metrics, aerospace and defence manufacturers can optimise equipment performance, reduce downtime, and maintain the highest standards of product quality. Using metrics such as these play a crucial role for aerospace and defence manufacturers in maintaining precision, safety, and adherence to strict regulatory standards.
Optimise your aviation and aerospace manufacturing processes with FourJaw.
Manufacturing metrics are essential for maintaining high-quality production and operational efficiency in the automotive industry. One of the key metrics used is Overall Equipment Effectiveness (OEE), which assesses equipment effectiveness based on factors such as availability, performance, and quality.
Utilisation is another important metric, measuring the percentage of time that equipment is in use during planned production hours.
By closely monitoring OEE or utilisation, automotive manufacturers can identify bottlenecks, optimise production schedules, and streamline their manufacturing processes. This leads to increased overall equipment efficiency, improved production output, and reduced lead times, resulting in enhanced competitiveness.
Learn how automotive manufacturers can use FourJaw to improve their operational efficiency with our machine monitoring platform.
The food and beverage industry relies on manufacturing metrics to ensure food safety, maintain product quality, and enhance production efficiency.
A common metric used is Throughput, which measures the rate at which goods are produced, ensuring that production meets customer demand. Another valuable metric is Yield, which calculates the percentage of usable output from raw materials, thereby reducing waste in the production process.
By closely monitoring these metrics, food and beverage manufacturers optimise production rates, minimise wastage, and improve overall operational efficiency, leading to better customer satisfaction and increased profitability.
Improve the efficiency of your processes with manufacturing analytics for food and beverage production.
Subcontract manufacturers typically have tight production schedules. Therefore, utilisation and downtime are two of the most common metrics used in this manufacturing sub-sector. Optimising production capacity is essential for contract manufacturers: measuring utilisation allows them to reduce bottlenecks and lead times while measuring downtime is crucial for maximising productivity.
On-time delivery, which measures the percentage of orders delivered to customers on time is another commonly used metric by subcontractors. By closely monitoring utilisation, downtime, and On-Time Delivery, subcontract manufacturers can optimise equipment utilisation, ensure timely deliveries, and enhance customer satisfaction. This leads to increased business opportunities, positive customer relationships, and improved competitiveness in the subcontract manufacturing industry.
Sterling Machining is a precision machining company that specialises in the extrusion tooling and subcontract machining industries. It was founded in 2001 by three directors, who between them have more than 90 years of combined experience in the manufacturing and metal extrusion industry. With the aid of FourJaw's data-driven insights, Sterling Machining fine-tuned its operations, achieving remarkable revenue growth from £3.8 million to £5 million. These insights were pivotal in realising a 25% uplift in their machine utilisation rates. Learn more about the Sterling Machining success story.
Pharmaceutical manufacturing demands stringent quality control and compliance with regulations. Manufacturers in this industry utilise the Overall Equipment Effectiveness (OEE) metric to assess equipment efficiency and identify areas of improvement in production processes.
In addition, the First Time Right (FTR) metric is crucial, measuring the percentage of products passing quality control without the need for rework. By closely monitoring OEE and FTR, pharmaceutical manufacturers can optimise equipment performance, reduce downtime, and maintain the highest standards of product quality and safety and regulatory compliance.
Learn more about manufacturing analytics for medical device manufacturers.
Textile manufacturing relies on optimising production processes and minimising waste. Manufacturers track the Inventory Turnover Ratio, which measures the number of times inventory is sold and replaced within a specific period.
Additionally, the Throughput metric is crucial in measuring the rate at which textiles are produced, ensuring that production meets customer demand.
By monitoring these metrics, textile manufacturers can manage inventory efficiently, reduce material waste, improve overall production efficiency and maximise inventory margins.
Manufacturing Metrics: A Summary
To summarise, having the right manufacturing metrics help you to understand what you are doing well and not so well, enabling you to make informed decisions to improve processes where appropriate.
It is important to make sure your strategic organisational goals and KPIs are defined first, to ensure the right metrics are in place to help you measure and track the progress towards achieving those goals.
However, no matter what you manufacture, from our experience, the single most important manufacturing metric is to start by understanding how productive your machines are.
By understanding this metric, manufacturers can inform production and process improvements across their manufacturing operations.