- Generative AI will unlock new value for mainstream manufacturers
- Tech-enhanced humans to power the factory floor
- Cloud will become the dominant form of computing in manufacturing
- New regulations will spark a boom in sustainable manufacturing
Generative AI will unlock new value for mainstream manufacturers.
All manufacturers use data in some form today, and we see huge volumes collected from machines and IoT devices on the factory floor. New Generative AI tools will make it easier for manufacturers of all sizes and specialisms to identify problems and improve processes by automatically recommending actions from their data.
AI and machine learning will move mainstream in 2025, going beyond isolated pilot projects and large manufacturers with dedicated data teams. Generative AI could make predictive maintenance standard practice and support a raft of process improvements that drive quality, productivity and sustainability.
Tech-enhanced humans to power the factory floor.
Manufacturing needs skilled people, but the industry has a talent crisis that makes them harder to find and much more expensive. The best option is for manufacturers to enhance the productivity of their people with technology.
In 2025, many manufacturers will augment their people with a range of proven, practical, and intuitive technologies that make them more productive. They include smart devices to improve communication between the top and shop floors, AI to spot problems and drive decisions on the shop floor, automation, exoskeletons and semi-autonomous cobots for material handling tasks.
Cloud will become the dominant form of computing in manufacturing.
When we founded FourJaw in 2020, most manufacturers we spoke to used on-premise IT infrastructure in their factories. Since then, there has been a big shift towards cloud computing, a significant enabler of the smart factory movement. The cloud has become the default setting for new manufacturing technologies.
Although more manufacturers use the cloud to host their data and applications than on-premise IT today, we suspect most of their data remains in the factory as many manufacturers still rely on local hardware for older software. This hybrid approach will remain the case for some time, but given the typical lifespan of servers, we believe 2025 could be the year cloud becomes the dominant form of manufacturing computing, not just for users but the volume of data and applications, too.
Thanks to IoT technologies and cloud computing, manufacturers can capture real-time production data with ease and communicate on their shop floor to show data insights such as machine utilisation.
New regulations will spark a boom in sustainable manufacturing.
A wave of new legislation will drive an even greater focus on sustainability in factory settings. Until now, many sustainability initiatives have been driven by cost and ESG considerations. New rules such as the Carbon Border Adjustment Mechanism, which will be fully operational at the start of 2026, are putting regulatory and financial pressure on manufacturers to understand and reduce carbon emissions from production.
Manufacturers are increasingly looking at solutions to reduce wasted energy and carbon emissions.
Manufacturers need to know precisely how much carbon is emitted from every unit they sell. We are seeing a concerted effort from manufacturers to understand the energy usage by each machine and production process to ensure they can measure their carbon emissions properly.
Chris Iveson’s predictions draw on the work he and the team do at FourJaw, which supports over 130 manufacturers globally by capturing production data and turning it into actionable insight to enhance productivity, sustainability, and profitability, and his previous experience identifying and commercialising manufacturing technologies developed at the University of Sheffield Advanced Manufacturing Research Centre.
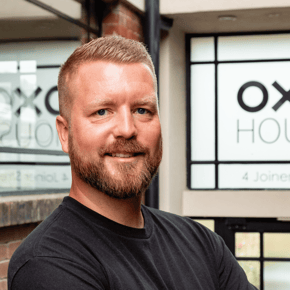