In manufacturing, 70% of digital transformation efforts fail due to low workforce adoption rates. So, what separates the winners from the rest? In this article, we explore real-world examples of manufacturers who cracked the code to successfully engage their workforce in adopting new digital tools and systems across their factories.
Background
The workforce plays a significant role in manufacturing excellence. Often, the difference between the success and failure of smart factory initiatives comes down to how willing and able a manufacturer’s people are to embrace new ways of working and the new tools at their disposal, and how well the organisation and its managers communicate around change.
A lack of experience in adopting technology and business cultures unfamiliar with embracing it can hamper transformation. Many manufacturers don’t have teams dedicated to finding and evaluating new tools, and almost half of those surveyed by Gartner expressed regret over recent technology purchases, citing:
-
Higher-than-expected costs
-
Implementation issues
-
Insufficient functionality
So, how do manufacturers ensure their teams are best prepared to embrace new technologies?
In this next section, we use real world manufacturing use cases to demonstrate how progressive manufacturers are implementing digital technologies by empowering their teams to be part of the cultural transformation.
Armac Martin: Upskilling for Adoption Success
By creating dedicated teams and upskilling employees, Armac Martin simplified technology adoption and ensured shop-floor operators were confident with digital tools.
Birmingham-based Armac Martin manufactures luxury brass cabinet fixtures and fittings for kitchens, bathrooms and bedrooms and is favoured by architects, interior designers, property developers and customers the world over.
Established in 1929, it is a fourth-generation family business that has grown through a continued programme of investment and a strong work ethic, today it operates around 20 CNC machines used for milling and turning and employs more than 120 people at its Birmingham-based facility.
Steven West, Head of Operations at Armac Martin, has created dedicated teams to help embed new technologies and upskill existing staff.
Armac Martin has focused on ensuring its workforce has the skills to deploy new technologies. It introduced new teams for developing and deploying digital solutions, staffing them through new hires and upskilling some existing employees. These teams focus on simplifying technology adoption to suit people with diverse skill sets and varying levels of digital literacy through training and support.
"When we’re deploying any new technology on the shop floor, we aim to work closely with the department where we’re deploying it. We ask for feedback and keep going back and checking they’re still able to use that technology. In recent years, we’ve introduced two new teams, technology and systems operations, responsible for developing and deploying digital solutions".
“The skill set in those teams is fairly new for us as a business and it’s one that we’ve acquired through new hires and developed with training and upskilling. That team has a very high skill set and a very technical skill set. When we deploy on the shop floor, we try to make things as simple and straightforward as possible so that anybody can interact with the technology.
"Our employees have a diverse skill set and varying levels of digital literacy. When we introduce new systems, we make it a priority to ensure our team are well trained and confident in using the system. We ensure we deliver training, provide documentation and check in with people to make sure they understand it".
AVPE Systems: Empowering Employees for Cultural Transformation
By integrating machine monitoring technology, AVPE Systems empowered its workforce to drive improvements, resulting in a significant cultural shift. Shop-floor operators embraced data-driven decision-making, reducing downtime and increasing efficiency without relying solely on management direction.
AVPE Systems, a leading aerospace component manufacturer, based in Bristol, UK, supplies customers throughout the UK, Europe and Asia with complex machined components for the aerospace industry, specialising in airframe and landing gear parts as well the machining of castings, forgings and 3D printed parts.
Like Armac Martin, AVPE Systems also focused on culture, as their Head of Operations, Sean Thomas explains.
Empowering employees to be part of the change and recognises that embracing technology has helped to transform culture:
"In this industry, everything comes back to whether people want to do a good job. What it [technology] has done is give people the feedback to improve. There’s been a huge cultural shift, particularly since implementing machine monitoring. Shop floor operators are now aware of downtime and can see its scale, and they want to help reduce it2.
"It’s helped to break that old-school manufacturing mindset. We find more and more now that the guys on the shop floor can make better decisions themselves without necessarily going up to management to decide what to prioritise because they can see the output and learn themselves".
FourJaw Insights
In this next section, FourJaw CEO, Chris Iveson highlights a critical factor for success: Communication. When operators understand how technology benefits them and the organization, they are more likely to adopt it. Manufacturers should start small, focusing on achievable wins, and gradually build confidence and momentum.
FourJaw has supported smart factory projects at more than 130 manufacturers around the world, the way new technologies are introduced is vital and we see that good communication and consistent frontline management as the most important success factors in cultural adoption:
“Technical skills in the workplace shouldn’t be an issue. We all have an smart phone in our pocket and we didn’t need a training course to learn how to use it. It’s the job of the tech providers to make beautiful and intuitive software that’s as easy to use as an iPhone. The bigger adoption problem is inertia: the willingness to try something new. Effective communication from management makes a big difference here. Operators need to know why there’s change, why we are monitoring now, and the benefits it can provide them. They need to be told that it is about continuous improvement across the organisation rather than monitoring them and their specific output".
Communicating the data insight with the entire team ensures everyone understands why and how the data insight is being used. It also creates a more inclusive culture and empowers staff to have a voice.
“Once you’ve had that conversation, then it’s about gradually introducing the technology and its functions, and consistency. Often, we see managers focusing on data labelling first, just getting machine operators to tag the causes of downtime accurately for a couple of weeks, and when they’re comfortable and seeing benefits with that, focusing on the next steps.
“Traditionally there has been resistance to trying new ways of working, so the best managers, once they’ve had those initial conversations, will check in with people if something’s not done, ask how they can help, and remind people why the technology is there to achieve and how it can make their jobs easier.”
It is impossible to overstate how influential culture is when adopting technology, and the ability of managers leading teams on the shop floor to encourage the use of new tools. The best managers will introduce new technology gradually and take time to explain why it is beneficial, both to the organisation and those shop floor operators, and how it can make their lives easier. They make those new technologies part of the furniture by checking in regularly to ensure people can use it properly and by celebrating initial wins and improvements people achieved by using it.
While some people need encouragement to make new technology part of their routine, others are inspired to drive their own improvements once they’re empowered with the visibility we provide.
Digital Transformation – Key Takeaways
Invest in Workforce Development:
Form dedicated teams to champion digital transformation and tailor training for diverse skill levels.
Manufacturers must prioritise developing the skills of their workforce to deploy and utilise new technologies effectively. Good practice includes creating dedicated teams to champion the deployment of digital solutions and providing training and support tailored to individuals with diverse skill sets and digital literacy levels.
Create a collaborative culture:
Foster open communication, involve employees early, and celebrate wins to build momentum.
Cultivating a culture that embraces technological change is essential for the success of smart factory initiatives. Manufacturers should define clear objectives and empower all employees to be part of the transformation process. Organisations can foster a culture where employees are motivated to adopt new technologies and drive continuous improvement by promoting transparency, encouraging collaboration, and providing feedback mechanisms.
Embrace Change Management:
Address resistance to change with clear objectives, consistent follow-ups, and support mechanisms.
Manufacturers must recognise the importance of change management in facilitating technology adoption. This involves addressing cultural barriers, such as resistance to change and lack of clarity in objectives, by promoting awareness, providing training, and facilitating open communication. By proactively addressing these challenges, organisations can ensure a smoother transition to smart manufacturing and maximise the benefits of technology investments.
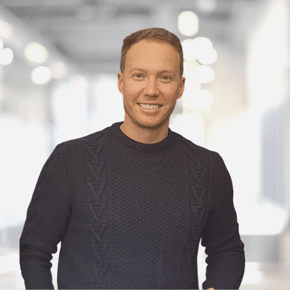