The UK aerospace sector is facing significant pressures as it navigates rising demand, supply chain disruptions, and a widening skills gap in the wake of the COVID-19 pandemic. These challenges are forcing manufacturers to rethink traditional capacity expansion strategies, driving a need for smarter, data-driven approaches.
Leveraging real-time data to unlock efficiencies has become an essential strategy for the sector to stay competitive, meet customer needs, and achieve manufacturing excellence. This article looks at the current pressures and the strategies aerospace manufacturers can take to overcome production backlogs.
Production Capacity Under Pressure
A combination of factors has created a perfect storm for the aerospace sector:
Rising Demand: As global demand for aerospace components and aircraft grows, manufacturers are expected to ramp up production quickly.
Post-Pandemic Supply Chain Disruptions: Continued supply chain uncertainties make it challenging for manufacturers to get essential materials on time, affecting production schedules and customer deliveries.
Skills Shortages: According to the Government Accountability Office (GAO), 88% of aerospace manufacturers report difficulty hiring skilled workers, limiting their ability to scale production effectively.
These challenges underscore the need for aerospace manufacturers to optimize their existing resources and find sustainable ways to increase output without over-reliance on expanding physical capacity.
What can aerospace manufacturers do to increase capacity?
Capacity Expansion Alone is Insufficient
Traditionally, manufacturers have addressed capacity needs by hiring more staff or investing in additional machinery. However, this approach brings its own set of challenges:
Over-Investment Risks: Expanding physical capacity without proper assessment can lead to unused resources and financial strain.
Labour Shortages: Finding and training skilled workers is a lengthy and costly process, and the availability of skilled labour remains low.
Slow Implementation: Installing new equipment and scaling operations can be time-intensive, further delaying productivity gains.
A mixed-capacity strategy, combining limited physical expansion with data-driven optimisation, offers a balanced approach to meeting these demands. Real-time data analytics helps manufacturers understand where current resources are underutilised, allowing them to improve production efficiency before committing to costly expansion.
Real-time data on machine utilisation, energy consumption, and downtime provides invaluable insights into production bottlenecks and inefficiencies.
Here’s how data-driven insights can address capacity challenges:
Uncovering Inefficiencies: Data from platforms like FourJaw enable manufacturers to measure productivity across various machines, identifying where resources are underutilised.
Diagnosing Root Causes of Downtime: Understanding specific downtime causes—whether due to maintenance, operator availability, or machine malfunction—empowers teams to address issues at their core.
Optimising Scheduling and Planning: Analytics-driven scheduling ensures resources are maximised, reducing idle time and allowing for more accurate production forecasting.
Energy Efficiency and Sustainability: Real-time energy monitoring can identify machines with high consumption rates, supporting both cost-efficiency and sustainability goals.
Use Case: Achieving Manufacturing Excellence through Data-Driven Optimisation
The true value of data-driven insights lies in their ability to empower aerospace manufacturers to take targeted action. By leveraging data, manufacturers can:
Identify and Minimise Downtime: Through visibility into downtime causes, manufacturers can proactively reduce machine inactivity. AVPE Systems, an aerospace component manufacturer, achieved a 30% increase in uptime by using FourJaw’s analytics platform to address and resolve downtime issues.
Inform Investment Decisions: Instead of rushing into capacity expansion, data allows companies to make informed choices about capital investments, ensuring new equipment will meet actual demand and production requirements.
Improve Staff Utilisation: When operators understand specific challenges through data, they’re better equipped to address issues, improving overall productivity and reducing frustration within teams.
UK Aerospace Manufacturing - Key Facts and Figures 2024
Supply Chain Visibility Gap: 69% of businesses report insufficient visibility over their supply chains, impacting their ability to manage capacity effectively.
Significant Workforce Impact: Difficulty in hiring skilled labour affects 88% of aerospace manufacturers.
Economic Contribution: The UK aerospace sector employs 110,000 people and contributes £37 billion to the economy.
Summary - Improve productivity & increase capacity with Data Insights
The aerospace manufacturing sector in the UK is at a pivotal moment. While traditional methods of expanding capacity remain relevant, a data-driven approach to optimising existing resources is essential for staying competitive and meeting rising demand.
Chris Iveson, CEO of FourJaw, stresses the importance of balancing ambition with practical steps: “Nothing kills technology initiatives like over-ambition. Moving too fast too soon creates more risk, wastes resources, and causes projects to grind to a halt. Smart manufacturers focus on quick wins first, such as boosting productivity and reducing energy use in a small number of production lines.”
By embracing data-driven insights and adopting a mixed-capacity strategy, aerospace manufacturers can navigate production backlogs, achieve manufacturing excellence, and secure a sustainable future in an evolving global market.
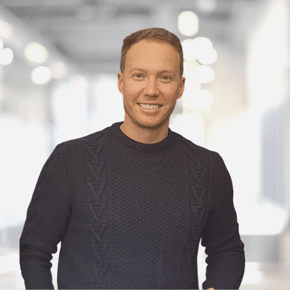