The manufacturing landscape is competitive, it always has been, but today, to be competitive on the global stage, manufacturers are facing various micro and macro pressures, and it is those who manage to navigate them that ultimately come out on top. These market conditions, and natural drive to want to stay on top are pushing companies to constantly seek new ways to enhance productivity, reduce costs, and improve operational efficiency.
Manufacturing analytics offers a powerful solution to these challenges, enabling manufacturers to harness data-driven insights to transform their operations. But what exactly are the benefits of manufacturing analytics, and how do companies implement them to achieve measurable results? In this blog, we explore the “what,” “why,” and “how” of manufacturing analytics, using real-world case studies from FourJaw’s customers to showcase the value.
What is Manufacturing Analytics?
Manufacturing analytics is the practice of using data generated from machines, processes, and operators to gain valuable insights into production performance. By collecting and analysing real-time data, manufacturers can identify inefficiencies, bottlenecks, and opportunities for improvement. These insights help them make informed decisions that lead to better resource utilisation, higher output, and optimised workflows.
Image: Steven West, Head of Operations at Armac Martin looking at machine utilisation data in FourJaw's management dashboard.
Why Do Manufacturers Need Data Analytics?
The key driver behind adopting manufacturing analytics is the growing need to stay competitive. Companies across various manufacturing sub-sectors - such as aerospace, automotive, and medical devices - face increasing pressures from rising customer expectations, stringent regulatory environments, and the demand for cost efficiency. Put simply, manufacturing analytics enables organisations to:
- Reduce Downtime: By pinpointing the causes of machine downtime, companies can minimise disruptions and increase machine utilisation and overall equipment effectiveness (OEE).
- Enhance Productivity: Analytics provide visibility into production processes, helping companies optimise workflow and reduce cycle times.
- Improve Quality: By tracking key performance indicators (KPIs) and monitoring deviations, manufacturers can proactively address quality issues before they escalate.
- Data-Driven Decision Making: Manufacturers gain the ability to make evidence-based decisions, reducing reliance on guesswork and subjective assessments.
How Do Manufacturers Benefit from Analytics?
In today's competitive manufacturing landscape, the pressure to increase efficiency while minimising costs is relentless. That's where manufacturing analytics, like those offered by FourJaw, come into play.
By providing real-time visibility into machine performance, manufacturers are able to boost productivity, reduce downtime, and make informed decisions based on actionable data insight.
Unlocking Efficiency and Growth with Manufacturing Analytics: Real Stories from the Factory Floor
Let’s dive into some real-world examples from companies that have successfully implemented FourJaw’s manufacturing analytics platform:
- Medical Device Manufacturer: Improving Compliance and Quality - Vernacare, a global healthcare manufacturer, drastically reduced machine downtime by 20%, removed production backlogs, and improved their on-time delivery rate. Their transformation was powered by real-time insights that allowed them to tackle inefficiencies head-on.
- Aerospace Manufacturer: Increasing asset utilisation and supporting Continuous Improvement strategy - SPS Technologies, a leading aerospace component manufacturer, identified 273 lost productive hours per week, resulting in a 23% increase in productivity after using FourJaw's platform. This not only helped in optimising existing resources but also unlocked significant potential for scaling operations.
- Luxury goods Manufacturer - Reducing Downtime and Increasing Output - Armac Martin, a luxury brass homeware manufacturer struggling to meet production demands, managed to boost their production capacity by 65% through FourJaw's analytics solution, giving them a competitive edge without the need for substantial capital investment.
How Does FourJaw’s Manufacturing Analytics platform work?
Image: © Drawing to represent how FourJaw's IoT manufacturing platform works.
At the heart of manufacturing analytics is data collection from machines via IoT hardware such as FourJaw’s MachineLink. This data is fed into a user-friendly platform where manufacturers can monitor key performance indicators in real-time. Armed with this insight, manufacturers can not only prevent issues before they become costly but also drive continuous improvement by consistently analysing trends in machine performance and operator behaviour.
Click here for a more detailed overview of how the platform works.
Conclusion: Manufacturing Analytics drives productivity and provides a competitive advantage.
Manufacturing analytics isn’t just a trend—it’s the future of efficient, smarter manufacturing. By implementing analytics, manufacturers can unlock the full potential of their operations, leading to cost savings, better quality-on-time products, and higher productivity, enabling them to remain competitive in their home market and on the global stage.
As the manufacturing case studies in this article show, adopting manufacturing analytics is a game-changer for companies across, no matter their manufacturing sub-sector. Whether it’s through reducing downtime, improving quality control, or empowering workers with data insights that replace opinions with facts, the benefits are clear.
By embracing data-driven strategies, manufacturers can not only survive in today’s fast-paced environment but also thrive.
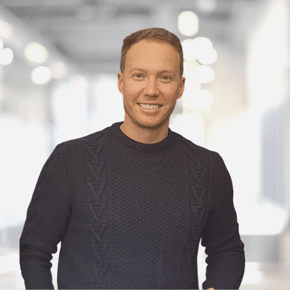