In the past decade, the manufacturing industry has undergone a remarkable transformation. Emerging technologies such as automation, robotics, and the Internet of Things (IoT), coupled with advancements in cloud computing, have revolutionised production efficiency and become more accessible to manufacturers of all sizes.
Research revealed in our 2024 Digital Excellence in Manufacturing report by business ISP Beaming, shows that more than half (55%) of manufacturers had already embedded multiple technologies such as AI, automation, data analytics, and cloud computing into their operations in some form by the start of 2023. Another third (35%) planned to introduce new tools to enhance insight and operational performance by the end of this year.
These technological advancements are boosting efficiency and reshaping decision-making on the factory floor. The impact of these developments is profound, from enhancing productivity to aligning smaller manufacturers with their larger, tech-savvy customers.
Automation: more affordable and user-friendly
Advanced technologies such as automation and robotics, once considered out of reach for many smaller manufacturers, are now much more affordable and accessible.
Automation has attracted significant attention: over a quarter (29%) of manufacturers planned to introduce technologies to streamline repetitive tasks and enhance efficiency for the first time in 2024. That would increase adoption to over 90%.
“I have been in engineering for about 15 years, and in that time, I think the biggest shift I’ve seen is towards automation,” says Stuart Cook, who was previously the Production Manager at Hydrafeed and one of several FourJaw customers we interviewed for our Digital Excellence in Manufacturing report.
“The shortage of staff and increasing skills gap we currently have within the industry are tricky to deal with. If you can’t recruit and you don’t have enough people to keep workshops running, the obvious solution is to use robotics and automation, so you can then keep the same amount of machines going with fewer people,” he adds.
“The thing for us is not necessarily the improvement in automation technologies, but the costs are decreasing, and they’re getting more user-friendly,” says Sean Thomas, Head of Operations at AVPE Systems. “We’re starting to look at the use of robotics to compete with lower-cost countries entering the aerospace market. Cost is extremely important in this industry.”

The inevitable wave of AI in manufacturing
As automation becomes more commonplace, the next wave of transformation is the integration of artificial intelligence (AI). AI’s potential to enhance decision-making, improve productivity, and address staffing challenges is widely recognised. 71% of manufacturers surveyed by Beaming already use it.
Stuart Cook believes AI could significantly impact the industry: “It’s everywhere at the moment, and I think it’s inevitable that with it being such a great tool, it has to be incorporated into the engineering and manufacturing world at some point. That will be the next big step.”
Armac Martin, a manufacturer of luxury brass cabinet hardware, is one of the many manufacturers to have already started using AI. “Part of our strategic growth has been to continue to develop our technology,” adds Steven West, the company’s Head of Operations. “We’ve introduced automation and machine learning, particularly in the last couple of years, that enable us to remove arduous administrative tasks. Those processes can now happen in the background.”
WATCH:
How manufacturers are using technology to drive Operational Efficiency
Empowering humans with data Insights
Alongside automation and AI, there is also huge power and interest in harnessing data. Data analytics and business intelligence tools, which many in the industry now consider essential for driving productivity improvements, are also expected to reach 93% of manufacturers this year.
“We have lots of sources of data, lots of machines, lots of suppliers, lots of customers, and bringing that all together from lots of different formats is really critical,” says Adam Lucas, Head of Commercial at AVPE Systems. “We’ve moved from a world where there’s 1,000 different spreadsheets, 1,000 different tools. If we’re not on top of bringing that all together, then somebody else, if they’re doing a better job at that, will be a better competitor than we are."
“Our data-driven insights have enabled us to increase output through a period of exponential growth. We’ve had to upscale our operations to meet customer demand,” says Steven West.
“Those insights have enabled us to target specific areas in the business where we know we have restrictions on our manufacturing, invest with technology, time or training, to upscale those departments and meet customer demand.”

“A lot of the wins to be had today on a manufacturing shop floor come from manufacturers using data and analytics to empower humans to work better and smarter,” says Chris Iveson, CEO of FourJaw Manufacturing Analytics.
“Having visibility of the way products flow through factories, and identifying the bottlenecks and causes of downtime that hurt productivity, allow continuous improvements that, added up, make a big difference. Once you have the data, you can take steps to eliminate the most common problems and determine the most efficient production schedules to maximise throughput.”
“It’s then you see automation and robotics come in, to do specific tasks where the data shows a machine can be more efficient and where people can make further gains by doing something more valuable instead,” adds Iveson.
Embracing the future of manufacturing technologies
The future of manufacturing is undeniably tied to emerging technologies. Alongside data, automation, IoT, and AI are transforming how manufacturers operate, making processes more efficient.
As these technologies become more accessible and user-friendly, the potential for even greater advancements is on the horizon. For manufacturers of all sizes, the key to future success will be the strategic adoption of these innovations, ensuring they remain competitive in an ever-evolving market.
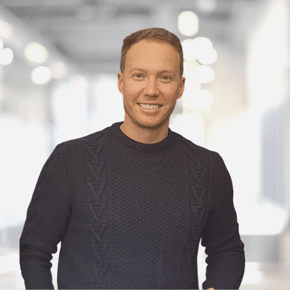