Increasing manufacturing production capacity is essential for companies looking to meet customer demands, keep up with competitors, and deliver worthwhile returns on investment.
This comprehensive guide outlines several ways to drive production capacity, covering the Six Big Losses, relevant measurements, calculations, metrics, and more. You’ll also find a variety of frequently asked questions answered by industry experts.
What is production capacity?
Production capacity refers to the maximum amount of product that a manufacturing facility can produce in a set period of time. Having sufficient production capacity is essential for manufacturers to meet the demands of customers and achieve operational goals.
Measuring capacity in manufacturing
Measuring manufacturing capacity is essential to understand how much product can be produced in a given period, allowing manufacturers to accurately predict lead times, order the right parts in time, schedule staff, and so much more.
Manufacturers can determine their ideal level of capacity utilisation by examining their current capacity and maximum capacity levels. This can help them establish goals to achieve optimal capacity and maximise their productivity.
There are several ways to measure production capacity, including machine utilisation, cycle time, and volume.
Machine utilisation
Machine utilisation measures the amount of time that a machine is in use compared to the total available time. This metric helps identify opportunities to improve machine usage and increase production. For example, if a machine has a utilisation rate of 80%, it means that it's not being used 20% of the time, highlighting an opportunity to increase production.

Cycle time
Cycle time is the time it takes to complete a production process from start to finish. By reducing cycle time, manufacturers can increase the number of products produced in a given period. For example, if a cycle time is 10 minutes, reducing it to nine minutes means that an additional product can be produced in that same period, increasing outputs and often, profitability.
Volume
This involves tracking the actual number of units produced over a specified period and comparing it to the maximum number of units that could be produced given the available resources.
What are the calculations for measuring capacity?
There are three standard calculations for measuring capacity:
Machine Availability - Hours
Machine Availability capacity: calculated by multiplying the number of machines available with the number of manned hours to operate.
The formula for calculating Machine Availability Capacity:
Machine Availability Capacity (MAC) = No. of Machines X Manned Hours
Production capacity for one component type
Production capacity for one component type: determined by dividing the machine availability capacity by the amount of time required to produce one unit.
The formula for calculating the Production Capacity of One component type:
Production Capacity = Machine Availability Capacity (MAC) / Time to Produce One Product
Production capacity of multiple component types
Production capacity of multiple component types: the production capacity is calculated for individual products and then added together to equal the total output capacity for all product types. To calculate this, we need to know the demand for each component type.
The formula for calculation of the Production Capacity of Multiple component types:
Capacity for Multiple Products = (Amount Product 1 X time to Produce Product) + (Amount Product 2 X time to Produce Product)
Traditional calculations of measuring capacity contain baseline assumptions either on the component cycle time or the current effectiveness of a manufacturing process. Keeping constantly changing cycle times up to date in the system is difficult, and machine effectiveness changes constantly based on things such as shift headcount, breakdowns and work-loading interactions.
This means that accurately measuring both capacity and lead times through a process is sometimes difficult to get right without adding large amounts of contingency into the plan, effectively creating waste or delivering late to customers.
Why is measuring production capacity important?
Measuring production capacity means that production teams can accurately predict lead times, improve production scheduling, better forecast cash flows and ensure the product is delivered to the customer on time. Ultimately, this will help increase customer satisfaction, productivity, and profitability whilst also reducing lead times and wastage.
Benefits of measuring production capacity
There are a number of benefits to measuring and increasing your factory's output capacity. Here are a few key advantages that FourJaw users have benefited from:
- Accurate/reduced lead times
- Improved workplace efficiency
- Better planning and use of resources
- Increased supply chain control
- Easily identify additional capacity opportunities
- More control over production operations
Manufacturers can use this framework to identify areas that are affecting production capacity and work to improve them. By identifying and resolving flaws in their manufacturing operation, managers can drive sustainable growth by using continuous improvement measures to increase efficiency, Overall Equipment Effectiveness (OEE) and output.
What are the Six Big Losses?
The Six Big Losses is a framework used in lean manufacturing that helps manufacturers identify areas of inefficiency in the production process. It was developed In 1971 by Seiichi Nakajima while working at the Japanese Institute of Plant Maintenance.
The Six Big Losses in manufacturing capacity are:
- Equipment failures
- Idling and minor stops
- Reduced speed
- Defects/Rejects
- Reduced Yield
- Setup and adjustments
Manufacturers can use this framework to identify areas that are affecting production capacity and work to improve them. By identifying and resolving flaws in their manufacturing operation, managers can drive sustainable growth by using continuous improvement measures to increase efficiency, Overall Equipment Effectiveness (OEE) and output.
How to Leverage the Six Big Losses
Once the Six Big Losses have been identified, manufacturers can implement countermeasures/process improvements to reduce or eliminate them.
The Six Big Losses align with OEE, so addressing them will have a direct impact on your OEE. Resulting in a reduction of Availability loss, Performance loss and Quality loss.
Here are a few strategies to leverage the Six Big Losses:
Equipment failures
Regular preventative maintenance and upgrades to equipment can reduce the frequency of failures and increase production capacity. Using a downtime logging system will enable you to understand how much equipment failures are costing you. This will give you the insight to make confident decisions, such as investing in preventative maintenance or replacing the machine with a new one.
Idling and minor stops
Improving communication between team members and implementing more efficient processes can reduce the amount of time wasted during idling and minor stops. Measuring machine downtime (stops), whether planned or unplanned, is an effective way for managers and operators to use data to take corrective action.
Reduced speed
Using machine monitoring to identify cycle times provides valuable insights to managers and operators, helping them to take corrective action, and ensuring cycle times that are slow, can be improved. Things such as investing in training, continuous improvement projects or putting more skilled operators on a job, are all examples of process improvements that can be identified when using machine monitoring.
Defects/Rejects
Implementing a quality control process and regular monitoring can reduce the number of defects and improve production. Using OEE and the Quality measure will provide a good benchmark of overall product quality. Since defects and rejects can occur from operator or equipment errors, regular training and checks will help to reduce waste.
Reduced Yield
During startup, a higher rate of defects is usually attributed to variation in the process. To mitigate this, it is essential to pay close attention to equipment settings and materials used in the production process. Higher inspection rates at the start of the shift and making use of quality control charts to capture drifting processes are effective ways of reducing variation in manufacturing.
Setup and Adjustments
To tackle setup loss, the SMED (Single-Minute Exchange of Die) program is a well-established and highly effective technique used in manufacturing.
The ultimate goal of SMED is to reduce the setup times to less than 10 minutes. Every aspect of the setup is carefully analysed to determine if it can be optimised in any of the following ways:
- Separated: Can it be moved before or after the setup?
- Converted: Can it be modified to move it before or after the setup?
- Streamlined: Can it be modified to reduce the time required to complete?
Through SMED, manufacturers can achieve significant improvements in their production processes.
6 Ways to Improve Production Capacity
Implement a lean manufacturing process
Lean manufacturing is a process that focuses on eliminating waste and improving efficiency. By reducing waste and improving processes, manufacturers can increase production capacity and reduce costs.
Invest in smart technology
Investing in smart technology can help improve production capacity by automating processes, reducing waste, and increasing efficiency. This could also mitigate the need to spend significant cash on capital investment by maximising the equipment already available today.
Automating your manufacturing systems can help streamline the production process, reduce human error, and offer more consistent, accurate results. Automated systems, such as machine monitoring also replace a lot of processes that would traditionally be manual and time-intensive exercises, therefore freeing employees up for more productive tasks.
Reduce downtime
By understanding the top reasons for machine downtime, managers, and supervisors can work with the operators to improve processes to minimise the amount of time that machinery or equipment is not in use, increasing overall efficiency and output.

Increase shifts
Adding extra shifts is a viable option to increase immediate or short-term capacity in factory output, although it can be expensive if it means paying overtime. Another option, if you have a production line that doesn’t require continuous operator attention, is to utilise ‘lights-out-manufacturing’ between ‘normal shifts’ provided that the facility does not already operate 24/7. Typically, lights-out manufacturing doesn’t require the labour a ‘normal shift’ would and therefore is a cost-effective way to increase capacity.
Reduce defects through a quality control process
Implementing a quality control process and regular monitoring can reduce the number of defects and improve production. Quality control processes help to identify and address any issues before they become a problem, allowing for more efficient and streamlined production.
The first step in implementing a quality control process is to assess the current process and identify any areas where defects are occurring. Once the problem areas have been identified, corrective actions can be put in place to reduce or eliminate these issues.
Two common methods to support quality control include:
Statistical Process Control, or SPC, is a method that tracks production metrics to monitor and control quality, enabling quality managers to detect and resolve issues before products are shipped.
Manufacturing Process Control Charts can be used to understand the process drift over time, by measuring components at set intervals (such as 1 in every 5) the process can be quickly monitored to understand its capability. It can also capture process drift with a view to correcting it before the non-conforming product is produced.
By combining with lean tools such as Total Productive Maintenance (TPM), 5S, and Kaizen, defects can be significantly reduced or eliminated altogether.
Machine Monitoring Software
As we have touched on briefly in this article, machine monitoring software, such as FourJaw enables manufacturers to improve a number of manufacturing processes. By providing real-time data insight into the current productivity levels and using key metrics such as utilisation and/or Overall Equipment Effectiveness, manufacturers can increase their production capacity.
Managers, supervisors, and operators can then use the data to take corrective action which will have the biggest impact on improving efficiency and production capacity.
Take the example of UK manufacturer, Armac Martin. A successful and highly regarded manufacturer of luxury brass cabinet fixtures and fittings, operating around 20 CNC machines. However, they had an issue. Squeezed production capacity was slowing growth.
The company’s strong reputation, high-quality product range and commitment to quality had resulted in a recent period of high demand and strong growth – but demand was outstripping supply and beginning to choke the production line.
The higher sales were welcomed, but the management recognised that due to increased lead times, they were in danger of not being able to fulfil orders and potentially losing sales. There was also the added risk of this having a negative impact on its reputation.
The Armac Martin management team felt the business had more production capacity but had no quantifiable measure of where that capacity was. They felt that a machine monitoring solution would provide the answer and turned to FourJaw for support.
Very quickly the data captured by FourJaw highlighted which machines were being well-utilised and in high demand, and those that were under-utilised and whose function was becoming redundant. The data provided Armac Martin with clear visibility of the production schedule and machine capacities.
Over the last 6 months, FourJaw machine monitoring software has enabled the Armac Martin Turning section to go from a 21.7% machine utilisation rate up to 35.8% today. An increase of 14.1% utilisation, but even more impressively – in terms of capacity.
As an example, in the time it would take Armac Martin to make 100 parts in April, they are able to make 165 parts today, an increase of 65%.
Read the full case study here or watch the video below.
Increasing production capacity - the metrics
Increasing manufacturing capacity in the short term can be both costly and risky. If production runs last longer than planned, overtime can become a massive expense and late or under-delivered orders can cause lasting reputational damage with customers.
A cost-effective way of maximising capacity is to deploy a machine monitoring software capable of capturing, analysing, and contextualising production data. By leveraging real-time, accurate data, factory managers can gain a deeper understanding of their operations and identify opportunities for improving performance.
There are several key metrics that management can use in order to effectively increase output; OEE, TEEP and Utilisation. These metrics offer valuable insights into the factors that influence production output and can help drive operational efficiency. By analysing these metrics, manufacturers can identify areas for improvement and achieve maximum production output.
OEE
Overall Equipment Effectiveness (OEE) measures the effectiveness of production equipment by tracking availability, performance, and quality. By analysing and tracking OEE, manufacturers can identify inefficiencies and bottlenecks in their production processes and implement improvements to boost performance.
Leveraging manufacturing analytics software such as FourJaw enables manufacturers to harness the power of OEE, optimise their operations and increase output. By monitoring machine data in real time, FourJaw provides manufacturers with the data-driven insights they need to optimise their operations, boost productivity, and reduce costs. Businesses can achieve greater operational efficiency, reduce downtime, and increase their production capacity, ultimately driving greater success and profitability.

TEEP
Total Effective Equipment Performance (TEEP), is a powerful metric that incorporates OEE with the additional factor of schedule losses. Whilst OEE measures the productivity of planned production time, TEEP measures the equipment's effectiveness throughout all available hours. A TEEP score of 100% indicates maximum possible production, with no downtime or equipment idling.
Utilisation
Utilisation is the time that the machine is productive (uptime) as a percentage of all the available time. It can be shown as a percentage of all the available time or in raw hours.
Through careful analysis of utilisation rates, manufacturers can identify areas for improvement and make informed decisions to help increase output without the expense of adding additional machines or labour.
Maximising utilisation requires a deep understanding of production processes and the factors that affect them, including equipment downtime, process bottlenecks, resource availability, and much more. With the help of manufacturing analytics software and real-time data monitoring, manufacturers can gain data-backed insights into these factors and take the necessary action to optimise production and increase utilisation rates.
Summary - The importance and value of increasing production capacity in manufacturing
Increasing production capacity is essential to meet customer demands and achieve overall business goals. Through the accurate measuring of production capacity, informed leveraging of the Six Big Losses, and the implementation of strategies to improve production processes, manufacturers can efficiently increase their production capacity and drive continuous improvement to increase productivity and profitability.
FourJaw’s machine monitoring software is trusted by manufacturers spanning multiple industries, including Oil & Gas, Automotive, Chemicals, Metal Product Manufacturing, Food Production and many more to increase their production capacity.
Our manufacturing analytics software is an affordable and accessible technology designed to allow manufacturers of all sizes to achieve their productivity potential. Installation is quick and doesn’t disrupt your factory floor thanks to its plug-and-play design, and best of all it works for batch and production workflows, regardless of brand, model or age, on any type of machine.
FourJaw’s manufacturing analytics platform provides a fast payback period with a return on investment typically achieved in months, not years. As you’d expect, our technology comes with customer support to make sure you and your teams get the most from the platform.
Get in touch if you would like to explore how FourJaw's machine monitoring platform can benefit your business!
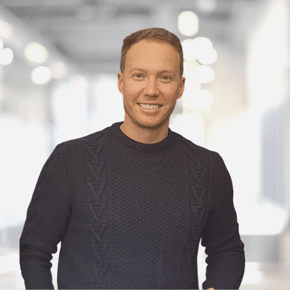