
CNC Machine
Monitoring Software
Award-winning CNC monitoring technology. Works on any machine, regardless of brand or model.
Connect Any CNC Machine, in Minutes.
FourJaw works on any CNC machine, regardless of age or type.
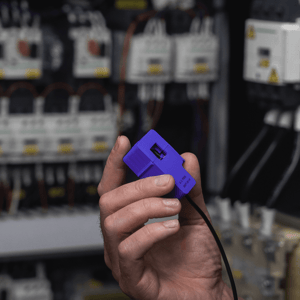
Clip the sensors to the machine's power cables.
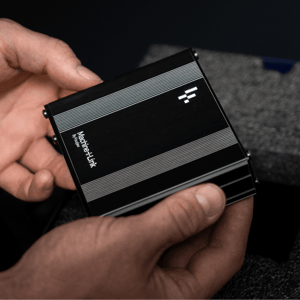
Connect the MachineLink IoT device to WiFi and mains power.
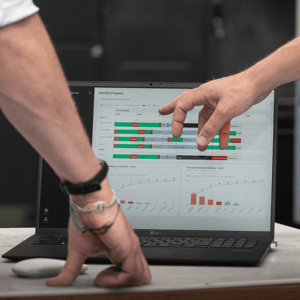
Use data insights to start identifying and removing inefficiencies.
Hassle-free CNC Machine Monitoring
Capture CNC machine performance data in real-time, automatically. Understand productivity and spot inefficiencies, no spreadsheets required.
Stay in sync with your shop floor. Track live CNC machine performance from anywhere, and keep production moving smoothly.
Monitor energy usage across your CNC machines. Cut waste, improve efficiency, and meet your sustainability goals.
Get instant alerts for CNC downtime and inefficiencies. Resolve issues quickly to keep machines running at their best.
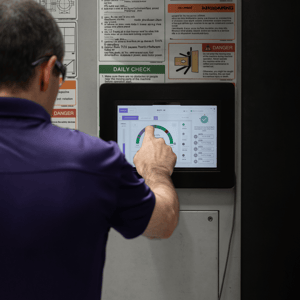
What Makes FourJaw Different?
Designed to seamlessly work with any and all CNC machines.
Works on any machine type, regardless of age or brand.
No large upfront costs. Choose to pay monthly or annually. Add more devices as required.
See your production data anytime from anywhere.
*FourJaw works with almost any machine that draws power. Because FourJaw doesn’t rely on PLC integrations, it’s brand-agnostic, making it ideal for manufacturers with machines of varying ages, brands, and types.
FourJaw Features
Boost productivity across your CNC machine shop. Whether you’re aiming to streamline processes, enhance precision, or cut costs, FourJaw delivers the insights you need.
Machine Utilisation
Get a live view of your factory floor. FourJaw automatically tracks machine status, downtime, and utilisation so you can act fast, reduce inefficiencies, and keep production running smoothly.
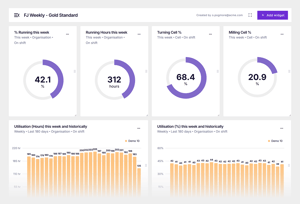
Production Timeline
Spot bottlenecks in real time with our Timeline View, and drill down to see exactly where production is stalling.
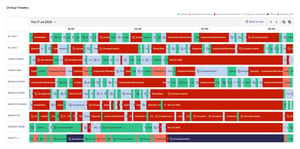
Energy Consumption Reports
Factories often waste energy unnecessarily, while facing increasing pressure to meet sustainability goals. FourJaw's sustainability features help you tackle both challenges at once.
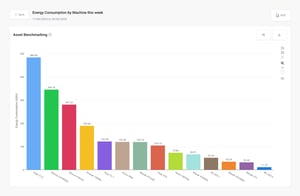
Customer Testimonials
"FourJaw has delivered a significant and sustained improvement in the productivity levels we're getting from our manufacturing centres."
Monitoring downtime, eliminating the various causes of waste in our processes, and deploying colleagues to where they are needed most has helped achieve a 30 per cent overall increase in uptime.
“FourJaw is helping us move towards 4.0 based on our S&OP.”
It allows us every month to analyse with the directors to see our strengths and weaknesses and plan forward based on what we find. From a continuous improvement point of view, we now have concrete evidence of where to focus our energy, helping with costings, budgeting and machine utilisation.
“We’ve removed all back orders and are now in a position to deliver orders on time for customers worldwide.”
This is a tangible benefit of our unprecedented increase in machine productivity, and we’ve also improved staff retention with a calmer, less stressful working environment where operators have the autonomy to get on with the job.
Visibility for you. Clarity for your Factory.
See how FourJaw transforms CNC machine shops like yours.
Watch our quick video to discover how FourJaw’s real-time machine monitoring helps you cut downtime, increase efficiency, and improve job tracking, giving you the insights you need to run a smarter, more profitable shop floor.
Try an Interactive Guide




See FourJaw In Action
Share your company details to request a personalised demo and discover the full potential of your factory.
Frequently Asked Questions
Find the answers to common questions about our CNC Machine Monitoring System.
Yes, FourJaw's Machine monitoring system is brand-agnostic, meaning it works with any type of CNC machine, including leading brands such as HAAS, Mazak, DMG Mori, Okuma, Makino, Doosan and Hurco (plus many more).
Another benefit is that our system works with mixed CNC machine fleets, so it doesn't matter if you have a mixture of brands, of different ages or types. Our CNC machine monitoring system will provide you with a single unified view of your factory floor.
Where conventional systems might read any spindle movement as "productivity", FourJaw accurately detects genuine, money-making productivity. For example, FourJaw can detect when a CNC machine is cutting metal, by observing the rise in current usage during actual work.
This not only provides a more accurate measure of machine efficiency but also ensures consistency in data across all machines, facilitating better decision-making across your factory.
In simple terms, machine downtime refers to any period in which a machine is not available for production. This can be categorised into two broad types:
Planned (productive) downtime: such as scheduled maintenance, changeovers, or quality inspections, which are controlled and
necessary to ensure smooth operations.
Unplanned (unproductive) downtime: sudden stoppages due to breakdowns, operator unavailability, supply issues, or other unexpected factors that disrupt output.
FourJaw captures downtime data through a combination of its MachineLink hardware and tablets mounted on the machines.
When a MachineLink detects downtime, it automatically prompts the operator via the tablet to select the reason for this downtime from a predefined list.
This process is quick and non-disruptive, designed to minimise interruption to the operator's workflow.
By simplifying the input method to just a few taps, FourJaw ensures that accurate downtime reasons are recorded with minimal effort, enabling a comprehensive analysis of machine productivity and downtime causes without impeding your operators.
Yes. Unlike traditional machine monitoring solutions, we designed our machine monitoring platform to be accessible, not only did we make it easy to install (minimising disruption to your factory floor) but we also made it affordable.
We offer monthly payment plans and you can install it yourself, so there are no high upfront installation costs often associated with traditional machine monitoring solutions